Think American steel is history? Not even close. Plenty of steel still comes straight out of U.S. mills—and yes, there are actual places cranking out everything from I-beams for skyscrapers to the rebar in your neighbor’s driveway. While the U.S. doesn’t flood the world with steel like China or India, it’s still a heavyweight in the game.
The big guys like U.S. Steel, Nucor, and Cleveland-Cliffs have massive operations dotted all around the country. And trust me, some of these plants are so high-tech, you’d barely recognize them compared to the old smokestack days. We’re talking electric arc furnaces melting down tons of recycled scrap, cutting down both costs and emissions—a win for budgets and the planet.
So why does it matter if your steel is made in America? For some, it’s about getting quality that’s easier to trace, supporting local jobs, or avoiding the supply chain headaches that can hit when you rely on overseas mills. If you’re hunting for genuine U.S. steel, labels like “Made in USA” can help, but don’t stop there—check into the mill certifications or ask suppliers for their source. Surprised? There’s more to this story than most folks realize, and some of it’s actually good news.
- The Short Answer: Is Steel Still Made in the USA?
- Who Makes Steel in the USA and Where?
- American Steel vs. Imports: What’s the Difference?
- Buying American Steel: What to Know
The Short Answer: Is Steel Still Made in the USA?
Here’s the deal—steel manufacturing is alive and kicking in the USA. It’s not just a handful of old factories clinging on. Right now, there are over 100 steel plants operating across the country. These places churn out millions of tons each year, covering everything from flat-rolled sheets to sturdy bars and fancy specialty steels. Just to give you a sense of scale, in 2024, U.S. producers made around 80 million metric tons of American steel. That’s not small potatoes.
Nucor, for example, isn’t just the biggest steelmaker in America—it’s one of the largest on the planet. Same goes for Cleveland-Cliffs, which now owns flagship facilities that send out steel for cars, bridges, and even your kitchen sink. U.S. Steel, a name everyone recognizes, still runs big mills in states like Pennsylvania and Indiana. No matter what you’ve heard, these companies aren’t museum pieces; they’re real businesses with thousands of jobs on the line.
If you want it straight from the experts, check this out:
“The United States remains one of the world’s top steel producers. Our industry supports more than 380,000 direct and indirect jobs.” — American Iron and Steel Institute
Want proof? Here’s a quick stats table:
Year | U.S. Steel Production (Million Tons) | Number of Active Plants |
---|---|---|
2024 | 80 | 100+ |
2018 | 87 | 120 |
Sure, America imports plenty of steel too—especially cheaper stuff from places like China or South Korea. But any way you slice it, made in USA steel still matters for big projects, national security, and local economies. If you’re ever on a job site and wondering if that girder or pipe is born and bred in the USA, there’s a good chance it actually is—at least if you’re buying from a reliable source.
Who Makes Steel in the USA and Where?
If you think all steel comes from far-off places, you might be surprised. Actual American steel makers are still running strong and scattered across the country. A few names pop up over and over: U.S. Steel, Nucor, Steel Dynamics, and Cleveland-Cliffs. These are the giants, and they’ve stuck around by getting smart—investing in new tech and keeping a close eye on quality.
U.S. Steel was born in Pittsburgh over a century ago, and it’s still a big player, with major mills like Gary Works in Indiana. Nucor is another powerhouse—they have dozens of steelmaking facilities, especially in the Southeast and Midwest. The cool thing is, they mostly use recycled scrap in electric arc furnaces, which is good for both the wallet and the planet.
Steel Dynamics keeps things moving in Indiana and Texas, while Cleveland-Cliffs made headlines buying up famous plants from AK Steel and ArcelorMittal USA (they even own that huge plant in Middletown, Ohio). There are also specialty outfits like Gerdau, making rebar in the South, and smaller regional mills handling niche products.
Here's a quick look at where the main action happens:
Steel Producer | Main Locations | Specialty |
---|---|---|
U.S. Steel | Indiana, Pennsylvania, Alabama | Flat-rolled, tubular |
Nucor | North Carolina, South Carolina, Arkansas, more | Sheet, bar, rebar |
Steel Dynamics | Indiana, Texas | Flat-rolled, long products |
Cleveland-Cliffs | Ohio, Michigan, Indiana | Flat-rolled, automotive |
Got specific steel needs? Don’t just look for the “made in USA” stamp. Ask for the actual mill certificate—basically, the steel’s birth certificate—for proof it came from a steel manufacturing plant here at home. Plenty of builders and manufacturers do this already as standard practice.
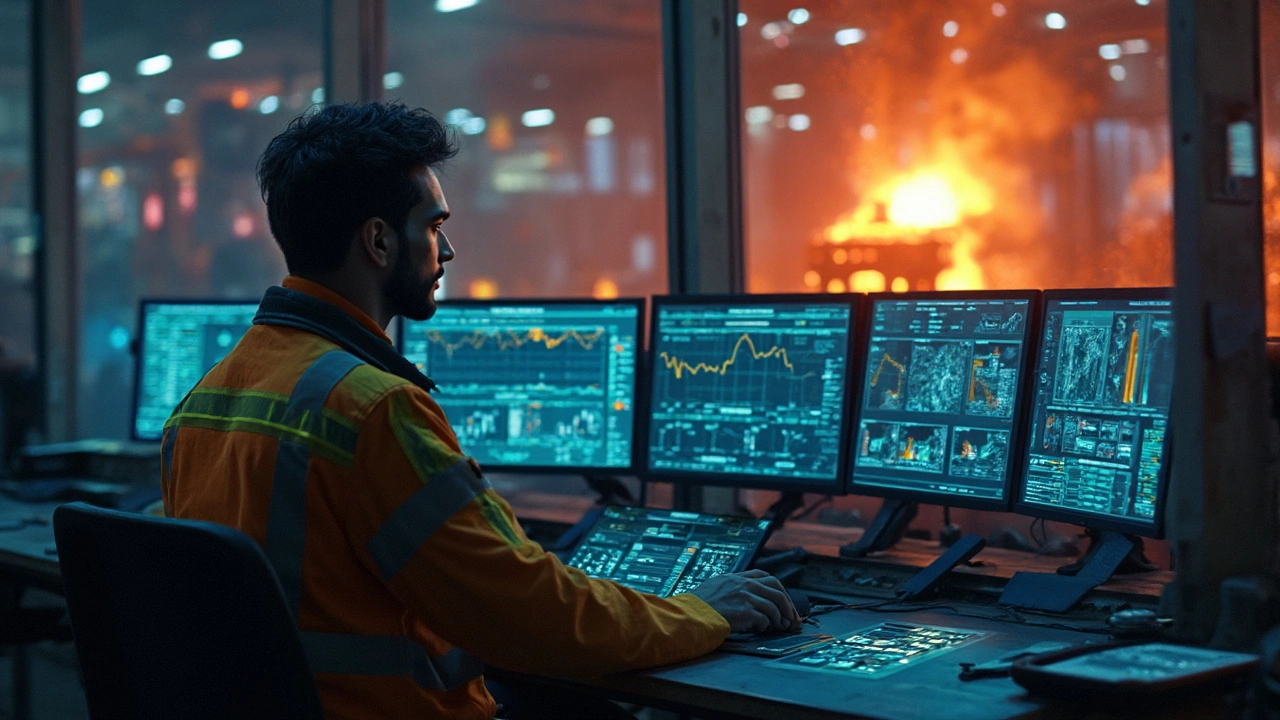
American Steel vs. Imports: What’s the Difference?
Here’s the real question everyone asks: why should you care if your steel was made in the USA or shipped from somewhere else? There are some clear-cut differences you’ll notice right away, and some that don’t get enough attention unless you’re knee-deep in a building project or running a fabrication shop.
First up, American steel is usually made to stricter standards for both quality and environmental rules. Factories in the U.S. follow industry certifications like ASTM and AISC, and they face tough EPA laws that many overseas plants just don’t have. That means you’re more likely to get material that matches up to what’s on the spec sheet—strength, durability, weld-ability, all that.
Now, price is a whole other story. Imported steel from places like China, Brazil, and Turkey is often cheaper up front. These countries have lower labor costs and less regulation, which lets them undercut U.S. prices. But sometimes that “bargain” steel brings up surprises—like being more prone to rust, or not meeting the grading you expected. American steel usually costs more, but what you pay for is a steady supply chain and a product that’s more traceable.
- Lead times: U.S. steel is faster to get, especially during global shipping crunches. Import delays can set projects back by weeks or months.
- Reliability: American mills give you easier access to customer support and replacement orders if anything’s off spec.
- Certifications: Projects needing “Buy American” compliance, like federal buildings or highway jobs, demand domestic steel by law.
Here's a quick look at cost and production stats:
Metric | U.S. Steel | Imported Steel |
---|---|---|
Avg Price/Ton (2024) | $950 | $730 |
Share of U.S. Market | 65% | 35% |
EPA Regulation | Strict | Varies (usually looser) |
Certifications | ASTM, AISC, Buy American | Depends on country |
So bottom line: going with American steel means more confidence in quality and usually a stronger supply chain, but you’ll pay a premium. Imports are easier on your wallet but can bring risks you’ll want to think through. If you’re working on a project where reliability, traceability, or legal compliance matter, domestic steel is pretty much non-negotiable.
Buying American Steel: What to Know
If you’re on the hunt for American steel, it takes a bit more than just trusting a sticker on the product box. The label “Made in USA” is a good start, but some imported steel gets processed or finished in America, which isn’t the same as steel made from scratch here. So, here’s what actually works if you want real steel made in the USA.
- Look for Mill Test Certificates (MTCs): Every reputable supplier should be able to provide an MTC or heat certificate that tells you exactly where the steel was melted, rolled, and made. Check for a U.S. mill location.
- Ask for Domestic Certifications: Steel made in American plants often comes with certifications like "Buy America" or "Buy American Act" compliance. These are especially important for government and infrastructure projects.
- Know the Big Players: Most domestic steel comes from names like Nucor, U.S. Steel, and Cleveland-Cliffs. If you see these mill names on your paperwork, you’re in good shape.
- Check with Your Supplier: Some suppliers blend foreign and domestic steel to cut costs. Don’t be afraid to get specific—ask: “Was this steel melted and manufactured in the U.S.?”
Pricing for American steel might run a bit higher than imports, but not always. Sometimes, global supply chain mess-ups or tariffs on foreign steel can actually make U.S.-made options a safer bet for price and reliability. Here’s a quick look at how production breaks down in the U.S. recently:
Company | Annual U.S. Steel Production (2024 est.) | Main States of Operation |
---|---|---|
Nucor | ~20 million tons | Arkansas, South Carolina, Alabama, more |
U.S. Steel | ~11 million tons | Pennsylvania, Indiana, Illinois |
Cleveland-Cliffs | ~15 million tons | Ohio, Michigan, Indiana |
If getting American-made steel is part of your bid, job, or project, nail down the details up front. Put it in writing, get those mill certs ready, and check with the project’s contract language. That way, you won’t end up with surprises, or worse, a load rejected for not being the real deal. In a nutshell? For true American steel, trace it back to the mill—don’t just take the shop’s word for it.