Picture this: the next time you're watching a skyscraper rise over the city or a massive sports stadium being built, you're actually seeing the handiwork of the biggest steel fabricators in the United States. Steel shapes the way we live—literally. But who tops the list as the largest steel fabricator in America? The answer tells you plenty about the nuts and bolts of American industry, plus a whole load of fascinating details about what keeps this sector ticking.
Meet the Giant: Who Holds the Crown in US Steel Fabrication?
When it comes to sheer size and output, one name beats all the rest: Schuff Steel Company. Founded back in 1976, they've become an absolute powerhouse, with projects stamped all across the American skyline. Based in Phoenix, Arizona, Schuff is actually a subsidiary of DBM Global—a holding that gives them a reach few can match. From gigantic stadiums in Los Angeles to energy facilities and iconic towers, they're practically everywhere steel matters. In 2024 alone, Schuff delivered more than 300,000 tons of fabricated steel. It sounds mind-boggling, but that's what it takes to lead in a country known for its mega-projects.
The scale Schuff operates on is hard to wrap your head around. Imagine a single fabrication plant that can churn out enough steel in one shift to frame a couple of city blocks. They've got more than a dozen fabrication shops scattered strategically from the coasts to the Midwest—there's one for just about any weather or logistical curveball. That reach isn't just about raw size; it means they can respond fast, whether it’s an NFL stadium contract or an emergency infrastructure repair.
What really sets Schuff apart isn’t just quantity, but capability. They specialize in complex, architectural steel—think swooping curves, giant cantilevers, or staggeringly tall columns. Their portfolio includes the Levi's Stadium in Santa Clara and the Salt Lake City International Airport. They've even been known to move their own teams on-site for field fabrication when precision or changing conditions demand it. The company is stacked with welders and engineers who have spent decades pushing what's possible in steel assembly.
But Schuff Steel doesn’t have a monopoly on the market. Others, like Banker Steel (now part of DBM Global), Canam Steel, and SteelFab, Inc., hold huge contracts and massive capacities. Every year, 'ENR' (Engineering News-Record) publishes a ranking of the largest steel fabricators by revenue, and the top five are often jockeying for position. For a bit of context, the full US structural steel market produces close to 46 million tons annually, and these top fabricators are responsible for a massive chunk of that.
Here’s something wild—fabricators like Schuff rarely just cut and weld. The process is almost like high-level project management. Complex supply chains, hundreds of in-house engineers, and networks of partnerships with local construction crews are all part of the mix. You could say these companies are as much about brains as they are about brawn.
The Art and Science of Steel Fabrication in the US
If you think 'steel fabrication' just means cutting beams and sticking them together, think again. It’s more like a massive puzzle, except every piece weighs several tons and tolerances are measured in microns. Fabricators take raw steel—rolled in American mills like Nucor or Steel Dynamics—and turn it into the huge frames that support stadiums, bridges, high-rises, and even roller coasters.
The process starts in the design phase. Engineers have to juggle load calculations, wind resistance, seismic codes, and all sorts of real-world oddities that might affect a structural frame. Modern fabricators rely heavily on 3D modeling software. Just twenty years ago, blueprints were covered in coffee stains and pencil marks. Today, a digital model lets the fabricator spot potential issues before a single piece of steel is cut.
Cutting has gone high-tech, too. Massive machines slice through beams with plasma or water jets, guided by computer programs that know exactly where each hole or notch goes. There's still room for good old-fashioned skill—welders need to hit exact specs to keep skyscrapers standing straight, and quality control specialists run endless tests to make sure nothing slips through. Twenty-first century fabrication often means robots handling repetitive or dangerous tasks while people focus on the tough, custom parts.
Most big projects are built off-site, in controlled factory environments. Once everything’s ready, the pieces move to the job site—usually on oversize trucks, sometimes even barges or trains for the truly gigantic stuff. Teams on-site bolt, weld, and secure these pieces with clockwork speed. Time really is money in construction, and delays can cost millions. The largest fabricators pride themselves on getting jobs done ahead of schedule and under budget, which builds a reputation that brings even more contracts their way.
Here’s a quick look at how the industry is currently built out (2024 numbers):
Fabricator | Annual Tonnage | Major US Projects |
---|---|---|
Schuff Steel Company | 300,000+ | Levi's Stadium, Apple Campus |
Canam Steel | 200,000 | SoFi Stadium, JFK Airport |
SteelFab, Inc. | 180,000 | Mercedes-Benz Stadium |
Banker Steel | 120,000 | Hudson Yards, One Vanderbilt |
The names change, but the demand never slows down. In a healthy year, American steel fabricators employ more than 80,000 people nationwide. Wages are solid, too—an experienced welder can pull in over $85,000 a year, plus generous overtime if they're willing to grind it out.
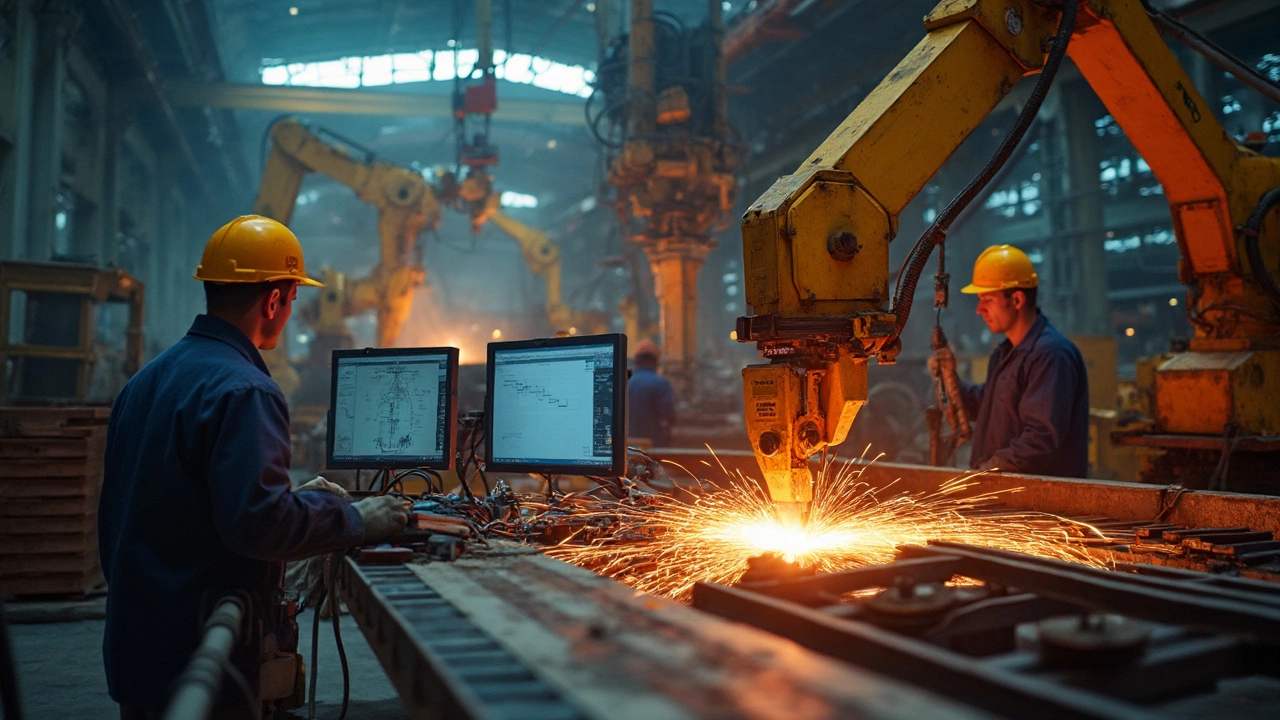
The Role of Steel Fabricators in Shaping Modern America
It’s hard to overstate how much these companies do to keep the country running. Take a step back and think about the bones of any big city. If you see a sports stadium, a hospital high-rise, or even large sections of freeway, chances are good a top-tier fabricator had their hands all over it. Even when Maya and I took a quick trip through Atlanta a while back, we noticed the new stadium there—a gleaming example of American steelwork. It's not just cities, either: enormous wind farm towers, pipeline infrastructure, and even some components for NASA launch facilities all start with specialized steel frames.
Fabricators are basically a quiet backbone for everything we take for granted. They’re behind the railways crisscrossing the country, the supply chain hubs at sea ports, and even amusement parks. Many folks don’t realize that steelwork is also essential for disaster recovery. After a hurricane or tornado, fast-acting fabrication shops swing into gear to replace damaged bridges and supports. Those rapid-response crews can make life livable again in record time.
The American steel fabrication industry also fuels a web of smaller businesses. Every town near a big project site ends up seeing activity in everything from trucking to engineering consulting. And since the sector constantly pushes for more automation, new jobs open up in robotics, IT, and software programming directly related to steel construction. It’s a perfect example of how a single big industry can ripple out across the whole economy.
It’s not all slow and steady, though. The business flips between wild booms and sudden slowdowns, often tied to government spending on infrastructure or waves of private investment. For example, the US government’s $1.2 trillion infrastructure package (announced in 2021) pumped a whole wave of new bridge, rail, and transit projects into the pipeline. Fabricators found themselves slammed with orders, especially for projects that want to highlight American-made materials—a huge point of pride in the industry.
No matter which way the economy turns, the role these companies play isn’t shrinking anytime soon. From software-driven design to on-site assembly crews who work in all weather, the scope keeps growing. And the biggest names keep finding new ways to take on projects that seemed impossible a decade ago.
Choosing a Steel Fabricator: What Matters for Major Projects
So, let’s say you’re a city planner, real estate developer, or even a logistics manager being asked to choose a steel fabricator. How do you separate the heavyweights from the pretenders? It’s not just about the biggest shop or the flashiest headquarters. The best fabricators check a bunch of critical boxes—and smaller project managers can actually snag world-class muscle if they know what to ask for.
- Project Experience: The top of the food chain—like Schuff, Canam, or SteelFab—have portfolios loaded with iconic stadiums, bridges, and airports. Check if they’ve delivered projects of similar scale or complexity to what you need.
- In-House Engineering: A deep bench of engineers and detailers means faster turnarounds and the ability to handle unexpected problems without delays.
- Plant Locations: Proximity matters. The closer the fab shop, the lower your transport costs and the more reliable your timeline—plus less exposure to weather or logistics mishaps.
- Quality Control: Certifications like AISC (American Institute of Steel Construction) are non-negotiable for safety and code compliance. But check for shop tours, QA documentation, and past performance on defect rates or recalls.
- Innovation Muscle: The best teams use modern modeling software and automation to detect errors before they happen. This is more important than ever for massive or unique jobs.
- Communication: The biggest projects always have curveballs. Pick fabricators who offer transparency, clear reporting, and direct lines for urgent issues. Half the nightmares in construction come from mixed signals.
And don't forget about financial muscle. Big projects mean big risk. You want a team that’s not going anywhere, even if there’s a bump in the road. Ask for references from similar projects, and get a sense of whether they’re known for sticking the landing—or just talking a good game.
In the world of US steel fabrication, size gets the headlines, but execution wins the day. It's no small thing to turn literal tons of metal into safe, beautiful, functioning structures that last a century or more.
If you ever catch yourself gazing up at a skyscraper or grand bridge, take a second to wonder about the work behind it. The biggest steel fabricators aren't just moving metal—they're shaping the country, beam by beam, and story by story.