Forget what you’ve seen in factory tour videos. Beneath the snappy conveyor belts and flashes of robotic arms is a world where minuscule missteps can ruin million-dollar batches. The most difficult manufacturing process isn’t just about heavy machinery or exact timings—it’s a place where physics flirts with the impossible, and nanometers matter more than anything. Think it’s a toss-up between making car engines and building airplanes? Neither comes close to the high-stakes world of semiconductor fabrication.
The Semiconductor Fab: Where Atoms Make or Break Everything
Walk into a semiconductor fabrication plant (most people call them “fabs”), and it feels a bit like stepping into a highly protected vault—except here, the villains are dust, static electricity, and cosmic rays. Chips, the brains inside everything from your phone to the satellites tracking your location, are built by stacking and etching tiny layers of material—sometimes just a few atoms thick. Sound tricky? The margin for error is laughably slim. To give you an idea, particles that would go unnoticed on a regular shop floor are deadly here. A single speck of dust, invisible to the eye, can obliterate a chip worth thousands. Keeping clean is so extreme that workers suit up in “bunny suits” that make Hazmat outfits look casual.
The real magic lies in the process: dozens of intricate steps, from chemical vapor deposition and photolithography to doping and etching, turn a millionth-of-a-meter-thin silicon wafer into the most complex thing humans make. Photolithography is insane—you shine light through custom stencils (called masks) to sketch circuit designs onto the wafer. But as those circuit lines shrink below 10 nanometers—thousands of times thinner than a human hair—the light itself starts blurring the lines, literally. That’s why fabs are chasing “extreme ultraviolet” (EUV) tech, where wavelengths are so short, engineers basically have to build new physics with each new generation.
Here’s something nuts: To make one computer chip, some fabs go through more than 1,500 steps, taking months for completion. Along the way, they face a horror list of problems—chemical instability, tiny vibration shocks, even minor temperature changes can sabotage the entire batch. And don’t even start on contamination. A 2019 study published in SEMI’s industry journal notes that most top fabs operate at “Class 1” cleanliness—fewer than 1 dust particle per cubic foot of air. Compare that to an operating theater in a hospital, which can have 10,000 particles, and you see the stakes.
Process | Precision Required | Common Risk | Time to Complete |
---|---|---|---|
Semiconductor Fabrication | Atoms/nanometers | Contamination, design flaws | ~3-4 months |
Boeing 787 Assembly | Millimeters | Component error, slow logistics | ~3-6 months |
Automobile Engine Block Casting | 0.05 mm | Inclusions, warping | ~2-4 hours (per block) |
Let’s face it—other manufacturing giants like airplane or car makers face complex coordination, but at the atomic scale, nothing beats fab. These multi-billion-dollar lines run 24/7, because downtime is catastrophic. Australia’s only commercial chip fab, in Sydney, admits a single broken filter can shut down operations for days.
What Makes a Process So Difficult?
So why are some processes exponentially harder than others? Start with scale. The smaller the product features get, the more the rules of everyday physics break down. Dust, static, electromagnetic interference, even someone sneezing in the next room can derail multi-step production. Next up—complexity. Some assemblies, like smartphone processors, cram billions of transistors into a space smaller than a fingernail. Every step has to play perfectly with every other, or the final product is scrap.
But there’s also this weird twist—innovation itself makes manufacturing harder. Once we master a process, someone invents a new material, a smaller pattern, or a faster circuit, and suddenly yesterday’s state-of-the-art facilities are barely “good enough.” An Intel fabrication engineer told IEEE Spectrum in 2023: “We’re fighting fundamental quantum limits now. Every cleanroom upgrade feels like a moonshot.”
Another nightmare: process variability. In food or auto manufacturing, you can use sensors and feedback loops to catch problems as they arise. But in chipmaking, feedback is too slow—you only find out you messed up three months and several million dollars later, when a wafer finishes processing. This lag makes “right first time” production almost unattainable.
Let’s not ignore cost and risk, either. A top-tier fab can cost as much as $20 billion to build. For each nanoscale improvement, new machines and tools are needed, which might only work for one product generation. That’s a headache for planners and bean-counters alike.
- Most difficult manufacturing process is dominated by yield loss—small goofs wipe out months of planning.
- Tool calibration often requires Nobel-level ideas. EUV machines, for example, use light sources hotter than the sun’s surface and mirrors with near-perfect smoothness—just for one step.
- Even with all this, global chip yields rarely top 70-80%. The rest becomes waste.
- Singapore’s Tech Manufacturing Institute found that a single faulty wafer might lose $100,000 in value. That’s why fabs spend millions on predictive software and sensors per year.
- Newcomers need years to get up to speed. The world’s newest fabs take up to five years just to get their yield rates near the industry average.
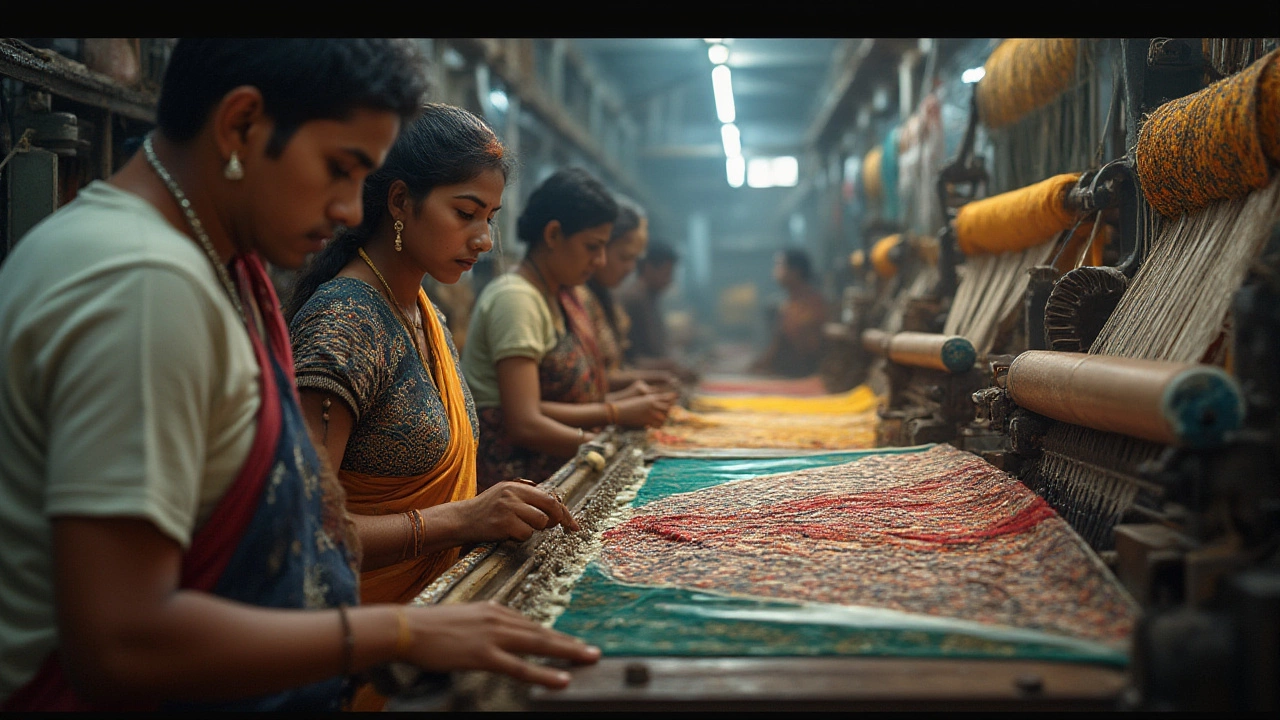
Tips and Practices to Survive High-Stakes Manufacturing
If you’re thinking about diving into the deepest end of advanced manufacturing, you’ll need more than nerves of steel. Precision and patience are your lifelines. Here’s what helps, straight from industry pros shaking down Australia’s rare but fierce chip facilities. First, obsess over environmental controls. Think air filtration, humidity, even floor vibration. Don’t go cheap—top boards monitor air with sensors that pick up on molecules smaller than you can imagine.
Second, make data your best mate. The top fabs use machine learning to catch process drift before it becomes a disaster. You’ll find entire teams whose only job is to analyze temperature, pressure, and particle statistics with the zeal of a dog after a bone.
Third, cross-train your workforce. When one machine acting up can sideline dozens of others, everyone needs to notice warning signs, not just the supervisor. Flexibility is vital because even the best-laid plans go sideways, often at 2 a.m. on a Friday.
Fabs also swear by strict change control. Altering a recipe, even minutely, needs double or triple sign-off. Rushing or skipping a step is usually the root cause of the “million dollar whoops.”
- Rotate your maintenance schedule, don’t stick to a fixed calendar—machines follow no timetable, especially at this scale.
- Reward workers for reporting near-misses. Most big fabs run anonymous logs so team members don’t fear blame games.
- Use “dummy” wafers to test equipment after repairs. If the machine messes up, better to scrap a $100 blank than a $10,000 part.
Funny enough, some of these practices—like rigorous cleaning—sound like things your grandma would insist on, but in fabs, those habits are gold. Take pride in being a neat freak; it could get you promoted faster than you expect.
Runners-Up: Other Insanely Difficult Manufacturing Processes
While semiconductors take the crown, other manufacturing worlds aren’t exactly a stroll in the park. Aerospace has its own unique chaos. Building a jet engine for, say, a Rolls-Royce Trent 1000 isn’t just plugging in parts. Every turbine blade is forged from “single crystal” nickel superalloy, shaped at 1,700°C, then cooled with air holes tinier than a strand of hair. Get a shape wrong, and the engine could melt down mid-air, literally. Since 2023, new engines also use composite ceramic blades, which adds another layer of “don’t mess up.”
Batteries, especially next-gen ones for electric vehicles, are now joining the pain party. You’re looking at assembly lines that operate in perfectly dry rooms—so dry, in fact, workers must hydrate before every shift just to function. A whiff of moisture in the wrong spot and boom—the cell is ruined, with a fire risk tossed in for good measure.
Precision optics, the stuff used in medical scanners and telescopes, comes close too. Grinding and polishing to atomic-level smoothness needs both deft hands and robots with zero room for error. In Sydney, there’s a medical lens firm that claims one faulty breath from a technician can add $10,000 in rework costs.
- Iron and steelmaking? Tricky at scale, but big errors are rare due to robust process controls. Sucks when a blast furnace goes offline though—restart costs can hit $1 million an hour.
- Pharmaceutical manufacturing? Sterility and chemical consistency are nightmares. The 2018 heparin contamination fiasco cost billions and proved how one slip-up in a drug plant can trigger global recalls.
- Even furniture manufacturing is tough at the artisanal level—sustainable sourcing and custom fabrication have their own headaches.
Yet, all of these share the common thread: as products get smarter, lighter, and more powerful, making them isn’t just about scale, it’s about outsmarting your own tools, processes, and sometimes, the laws of physics.
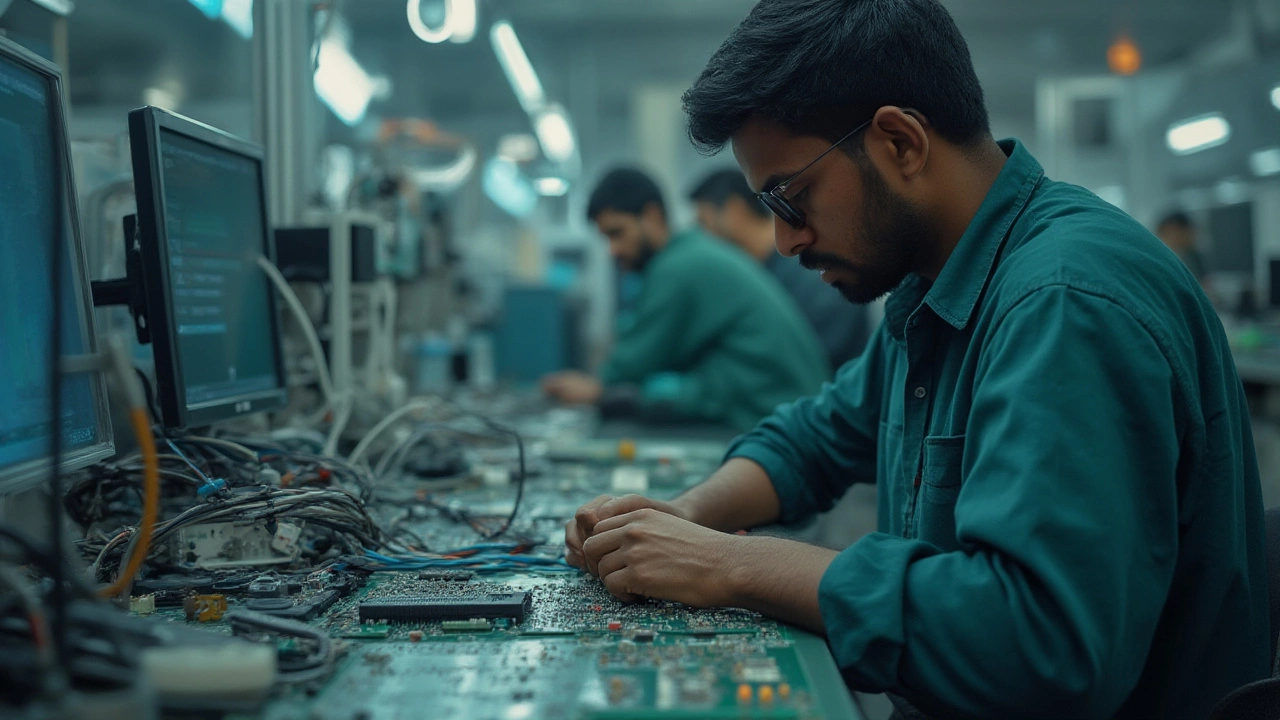
Where Is It All Heading? The Future of Difficult Manufacturing
We’re not seeing things get easier. If anything, the next few decades look even wilder. Moore’s Law—that prediction that chips double in power every two years—might be slowing, but customer demands aren’t. If anything, fields like quantum computing, biotech, or the next class of electric vehicles are asking factories to push boundaries even harder. Industry stats from 2024 show over $250 billion spent globally on new manufacturing gear, most of it to handle processes nobody had heard of five years ago.
AI is already poking its head into the fab world, sniffing out patterns no human could spot. Yet, while algorithms can flag problems, actually fixing them often takes a seasoned technician with years of scars and wisdom. That tradition isn’t fading anytime soon. Meanwhile, supply chains keep tightening. As seen during the COVID-19 pandemic and the recent 2024 raw material crunch, even a stuck cargo ship or cyberattack can halt the most advanced plant. This is why smart manufacturers are obsessed with local backup: you can’t be the best if you’re waiting for a shipment stuck halfway around the globe.
What about sustainability? That’s the next boss level. Chip fabs burn through millions of liters of ultra-pure water and gulp energy at shocking rates. The new game is making processes cleaner and greener, like recycling water or developing non-toxic chemicals. Australia has a federal push for “green fabs” by 2030—but getting there means more redesigns, more risk, and almost certainly, even steeper learning curves.
So, the most difficult manufacturing process keeps raising the bar, and every time you think humans have mastered it, someone drops a new wrench into the gears. The next breakthrough is just as likely to flash out of a university lab as from one of these super-controlled billion-dollar factories. The next time you tap your phone or start your electric car, remember: behind that magic is a process so tough it nearly breaks the people and machines who try to tame it. And that’s why those who master it? They rarely brag—they’re too busy catching the next dust particle about to blow everything apart.