Why does manufacturing in India, especially for chemical companies, keep tripping over the same hurdles year after year? Everyone talks about India being the next big thing, but reality on the ground feels stuck.
If you talk to anyone running a small chemical plant, the first thing they gripe about is paperwork. Getting all those dozens of licenses? It's enough to make grown men want to quit. Rules change often and can differ from one state to another. Instead of focusing on building or selling, factory owners drown in forms and approvals. That’s not just annoying—it's expensive and delays everything.
- The Hidden Cost of Red Tape
- Infrastructure: Stuck in the Slow Lane
- Policy Whiplash and Business Uncertainty
- Why Chemicals Face Bigger Headaches
- Ways Forward: Smart Moves for Growth
The Hidden Cost of Red Tape
This part gets real frustrating. Red tape is what slows down manufacturing india—ask any chemical business owner. Every step needs an approval, but it’s not just about ticking a box. Rules change by the district, and even by the day. A chemical plant in Gujarat might need different paperwork than one in Maharashtra. No one can keep up, not even those who deal with this for a living.
An average chemical manufacturer needs at least 45 clearances to start up. That includes environmental okays, factory licenses, safety nods, and a bunch more. The World Bank’s Ease of Doing Business Report put India at 63rd out of 190 in 2020—beating some neighbors, but still way behind where it could be for a country this size. India took 18 days on average to get a business up and running, but the behind-the-scenes hassle felt way longer, especially for chemicals.
And paperwork always comes with costs nobody talks about up front—legal fees, unofficial charges, wasted hours, and delayed launches pile up. To put it into perspective, a local industry survey shows that more than 70% of small chemical firms end up spending 15–25% of their total startup funds just on compliance and paperwork, not machinery or real operations.
Factor | Impact on Chemical Manufacturers |
---|---|
Number of licenses needed (avg.) | 45+ |
Percentage of startup funds to compliance | 15–25% |
Average time to set up (in days) | 18 (official), often 60+ (actual for chemicals) |
Rank in Ease of Doing Business (2020) | 63 |
This maze makes it easy to slip up and break a rule without even knowing it. Penalties or shutdowns can be sudden, and sometimes fixing a missed step needs another pile of forms. Some companies try shortcuts, but these can come back to haunt you with surprise inspections or sudden fines. No wonder many chemical businesses find it tough to even get started—before they sell one drop of product, they’re often already running out of cash and patience.
Infrastructure: Stuck in the Slow Lane
It's nearly impossible to talk about why India’s manufacturing isn’t happening at full speed without looking at our infrastructure headaches. If you manage a plant, you know exactly what I mean. Moving raw materials or finished chemicals across states often feels like a slow-motion marathon.
Let’s talk transport. India's logistics costs are about 14% of GDP. Compare that with China, sitting at around 8%. Trucks crawl across highways dodging potholes, traffic jams, and surprise tolls. Trains get booked months in advance, and ports are crowded with long wait times. All this eats up time and margins.
Power cuts are another regular story. Many manufacturers run their operations with backup diesel generators which jacks up the cost and, let’s be honest, kind of kills the vibe for any lean manufacturing plans. Reliable electricity is still a promise in many parts.
- Roads: 30% of India’s roads are still unpaved, especially near small-town industrial clusters.
- Rail: Freight speeds average 25 km/h — less than what people jog at in the morning.
- Ports: Logistics for exports or importing raw material can take several extra days here compared to, say, Singapore or Malaysia.
Check the numbers in this quick snapshot:
Factor | India | China | Germany |
---|---|---|---|
Logistics Cost (% of GDP) | 14% | 8% | 9% |
Average Freight Speed (km/h) | 25 | 35 | 50 |
Power Outage Days/Year (Manufacturers) | 25 | 6 | 1 |
For chemical manufacturers, these slowdowns are brutal. Many specialty chemicals spoil or degrade if delayed. Imagine getting a shipment of ingredients after a week stuck at a warehouse with no temperature control. It’s a nightmare.
So, tips for coping? Build relationships with multiple transporters, not just one. Invest in small-scale, in-house logistics. And if you’re not already tracking your supply chain digitally, now’s the time. The only way to beat slow lanes is to keep moving smarter than your competition.
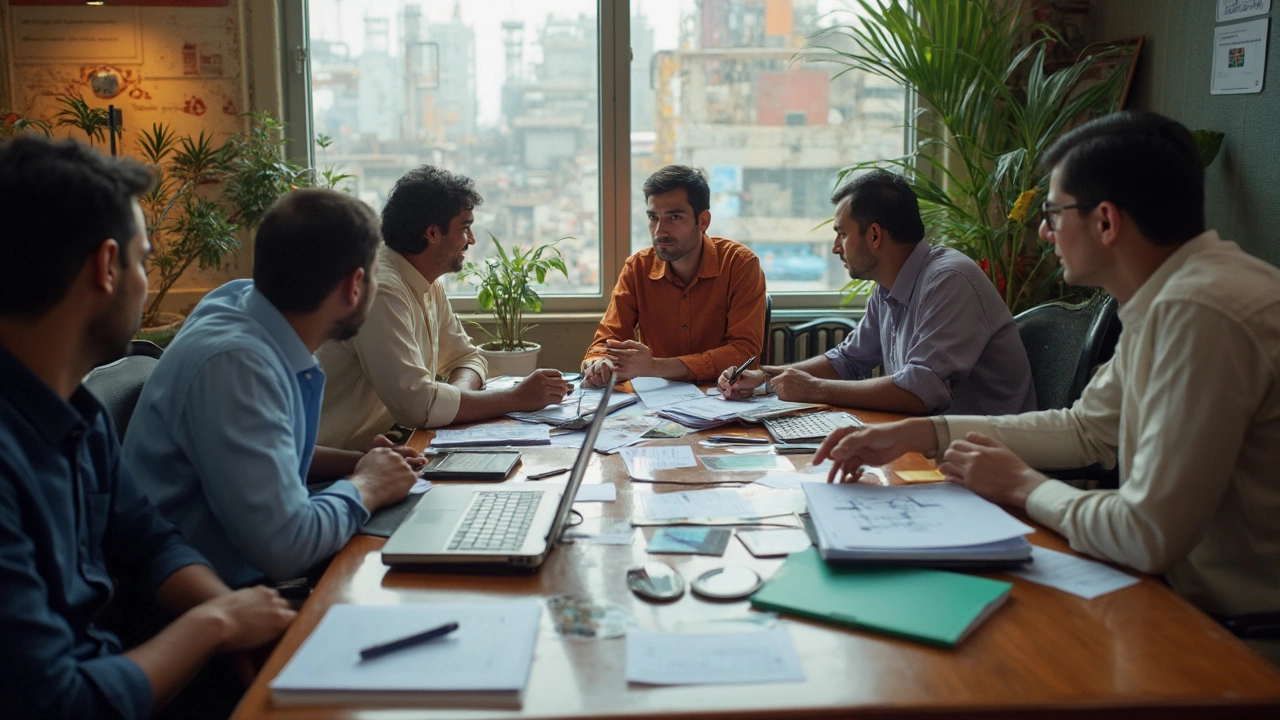
Policy Whiplash and Business Uncertainty
If you think setting up shop in India is just about building a plant, think again. The real headache for most manufacturing india bosses is living in a world where rules can flip overnight. Government policies around chemicals change faster than the weather. One year there’s a tax cut or an export incentive; the next, it disappears with barely a warning. For factories relying on long-term plans, that’s a nightmare.
Take the sudden ban on certain chemicals in 2024. Plants had inventory piled up, and out of nowhere, products became 'illegal.' No phase-out period, just a hard stop. Many businesses had to write off months of stock. When you can lose money overnight like that, it’s tough to invest or expand.
Import policies are another big tangle. Duties swing up and down, and sometimes even get rolled out mid-year. India still imports about 35% of its chemical inputs, so these shifts slam smaller manufacturers who don’t have backup suppliers or fat margins. Here’s a quick look at how unpredictable policies affect the chemical sector:
Policy Change | Year | Impact |
---|---|---|
Ban on specific industrial solvents | 2024 | Sudden stock losses for 200+ SMEs |
Import duty hike on key raw materials | 2023 | 10-15% increase in costs across small plants |
GST credit restrictions | 2022 | Cash-flow crunch for manufacturers |
So, what can businesses do? Keep a legal advisor handy and don’t put all your eggs in one basket—spread suppliers and diversify products if you can. Building a cash cushion helps, too, for policy curveballs. Sure, it’s extra work. But in India, safe is better than sorry, especially when it comes to policy whiplash.
Why Chemicals Face Bigger Headaches
If you think manufacturing is tough in India, try running a chemical business. It’s another level of stress. There are issues that hit chemical manufacturers harder than others, and most of them come down to safety, cost, and supply chains.
First up, there’s the huge headache around getting the right raw materials. India depends a lot on imports for basic chemicals. For example, over 40% of India’s chemical raw materials are shipped in from countries like China. When there’s a global supply hiccup or a sudden ban—like what happened in 2022 when China cut exports—Indian factories scramble and prices shoot up.
Year | China Import Dependency (%) | Domestic Supply (%) |
---|---|---|
2015 | 37 | 63 |
2020 | 41 | 59 |
2024 | 44 | 56 |
Then there's the red tape. Chemicals come with stricter safety rules (for good reason), so every step, from buying to handling and shipping, gets checked and double-checked. A single mistake can mean a factory shutdown for weeks or even months. But here’s the catch—the government’s safety checks still aren’t consistent from state to state. What passes in Gujarat might get flagged in Tamil Nadu.
Cost is another punch in the gut. Manufacturing costs for chemicals in India can be 15-25% higher than in Southeast Asian countries. Why? High power bills, poor bulk transport options, and taxes that pile up at every stage. Smaller businesses feel it worse since they can’t spread the costs like bigger brands do.
- High dependency on imports means sudden shocks.
- Strict but inconsistent regulations slow down production.
- Extra costs for compliance, power, and logistics eat into profits.
Add to this the constant need for new technology (some machines are simply not made here), and staying competitive looks even harder. For anyone thinking of getting into chemicals, it’s not just about knowing the chemistry—it’s surviving the maze of policies, costs, and supply problems that come with it.
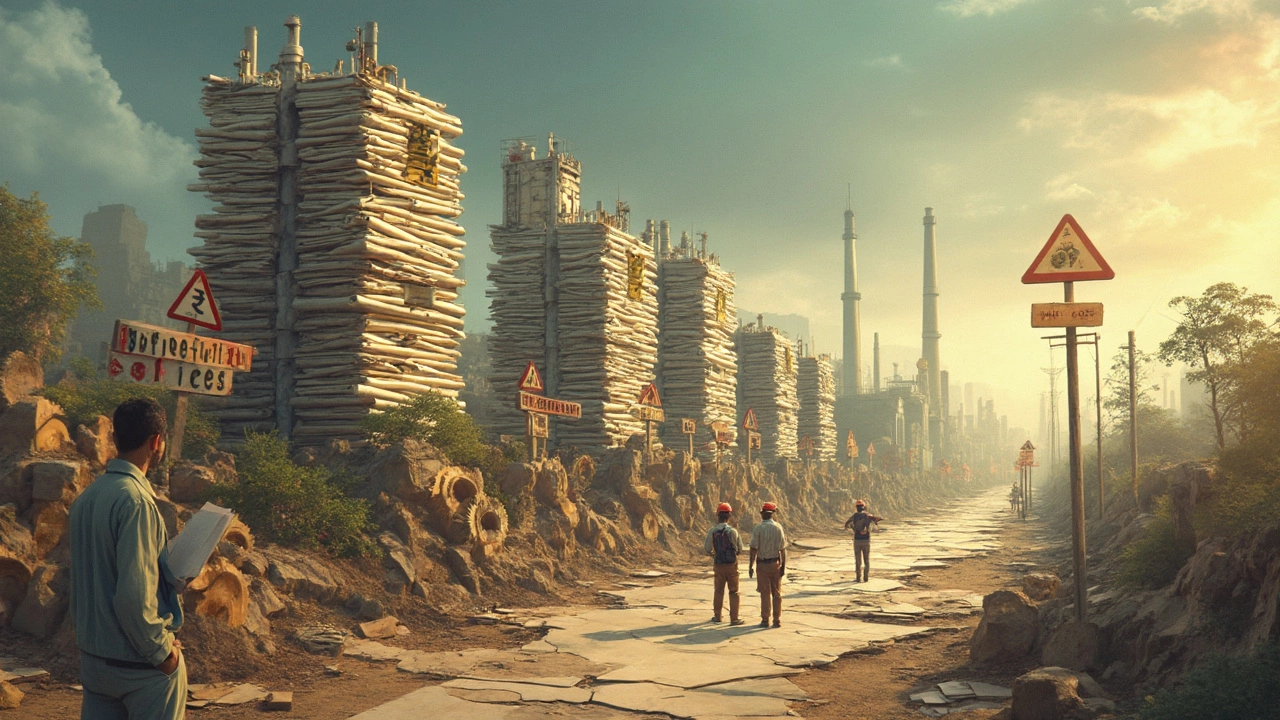
Ways Forward: Smart Moves for Growth
Let’s get real—waiting for some grand government masterplan isn’t helping chemical manufacturers in India break through the ceiling. But there are some moves that can actually push things forward, even if the system isn’t perfect.
First up: technology pays off. Plants using modern automation and digital tracking work faster, use less power, and waste fewer raw materials. According to the Indian Chemical Council, companies that went digital even in small ways cut operating costs by almost 20%. Think of it as insurance against sudden price spikes or new compliance rules.
Next, let’s talk about group action. One small chemical factory may struggle, but joining industry clusters or local associations helps businesses grab better deals for imported inputs, share logistics, and stay up-to-date on new laws together. Groups like the Gujarat Chemical Association have proved this isn’t just talk—they’ve pooled resources to lobby more effectively and get real improvements in port processes.
Another underrated trick? Build a proper compliance team. Regulatory headaches are less painful when you have people who actually watch for policy changes and talk straight to officials. It sounds boring, but it spells fewer fines and fewer shutdowns. Larger companies in Mumbai and Vadodara already do this, and even smaller players are seeing that an upfront salary cost saves crores in the long run.
- Upgrade systems to track chemicals and waste, so you aren’t caught out during inspections.
- Network with export-focused firms. They’re usually more tuned in to global quality demands and smoother shipping options.
- If managing cross-border raw material supplies, partner with reliable Indian suppliers—even if they cost more—to avoid port delays that mess up your timings.
And here’s the big one: don’t ignore staff training. Human error triggers over half of safety and compliance issues. Plenty of smaller companies now run monthly safety briefings and quick anytime refreshers on the shop floor. That drop in accidents shows up straight on the bottom line.
Most of these aren’t pie-in-the-sky ideas. They’re working for solid players in India’s manufacturing world right now. Step up on tech, join the crowd, stay on the right side of laws, and train people smartly—these moves beat waiting for perfect conditions every single time.