The steel industry forms the backbone of modern civilization, with its tendrils reaching far into both economic machinations and societal growth. As it stands today, the landscape of steel manufacturing is shaped by a handful of powerful players who steer the course for innovation and production. This dynamic sphere is not merely about forging metal; it is a complex interplay of geopolitical, environmental, and technological narratives.
Dive with us into the world of steel to uncover who holds the reins in this industry. From historical growth spurts to groundbreaking technologies driving sustainability, we'll cover the giants in steel production and explore the countries pushing the envelope of possibility. As we traverse through the stories of leading companies, technocrats, and environmental advocates, you'll get a clear picture of an ever-evolving sector that's central to our everyday lives.
- Historical Overview
- Top Steel-producing Countries
- Leading Steel Manufacturing Companies
- Technological Innovations
- Environmental Impact and Sustainability
- Future Trends in the Steel Industry
Historical Overview
Steel production has been a cornerstone of industrial advancement since its inception, weaving its way through pivotal moments in history. It's hard to overstate the significance of steel in shaping the modern world. Picture the 19th century when the newfound Bessemer process revolutionized steel manufacturing by drastically reducing costs and boosting production volume. This era marked the dawn of mass steel production, enabling the construction of railways and skyscrapers that transformed urban landscapes. Such advancements propelled nations like the United States and the United Kingdom to forefront positions in the industrial world. The adoption of the open-hearth process further extended these capabilities, proving invaluable for achieving the scale required for modern warfare and infrastructure development during the early 20th century.
As we moved into the mid-20th century, steel became the sinew of global warfare and peace-time reconstruction. The steel industry saw another evolution with the introduction of the basic oxygen furnace process, refining the quality and efficiency of steel production. This technological leap, combined with escalating demands during the post-war reconstruction, saw countries like Japan rising as unexpected powerhouses in the steel market by the 1960s and 70s. Japan's surge was a testament to the vitality and dynamism of the steel industry globally. Merely decades earlier, they were counted out, and now they had reshaped the landscape with superior manufacturing techniques and competitive pricing strategies.
In more recent years, the focus has shifted again. As information flows freely and technology accelerates the pace of change, we witness China emerging as the dominant steel-producing country. In 1996, China overtook the US in steel production for the first time, underscoring the changing tides in power and production capacities. Today, China produces more than half of the world's steel, with companies like Baowu Steel Group leading the charge. This realignment of power in the steel world is as much a story of economic policy as it is of raw production capability—a reflection of how strategic investments in infrastructure and technology can alter national trajectories significantly. A quote from noted economist Paul Krugman surmised,
"The rise of nations is often measured in tons of steel."This recognition of steel's role speaks to its irrefutable influence on economic power and national prosperity.
Top Steel-producing Countries
In the vast arena of the global steel industry, certain nations stand out due to their staggering production capacities and widespread influence. At the forefront sits China, an undisputed behemoth in the realm of steel production. The sheer scale of its output is nothing short of remarkable, often accounting for more than half of the world’s steel. This dominance is driven not just by internal demand but also by strategic initiatives aimed at global exports, making Chinese steel a staple in infrastructure projects worldwide. The government’s consistent efforts to modernize its production facilities and reduce carbon emissions have kept it a leader in innovation as well.
Close on the heels of China is India, the second-largest producer, which has seen impressive growth over the past decade. India's surge in steel production is fueled by its rapidly expanding construction and automobile industries, which demand both quality and quantity. The Indian government's policies, such as the National Steel Policy, aim to enhance infrastructure, promote domestic production, and support sustainability in processes. With vast iron ore reserves and a young workforce, India's potential in the steel sector is immense, setting it on a trajectory that might surprise traditional giants.
Japan, another industrial heavyweight, has maintained its position as a top producer despite facing challenges from emerging markets. Japanese steel is renowned for its quality and technological innovation. The nation's steel companies are pioneers in developing high-grade steels that contribute to advanced engineering and automotive industries. Despite the hurdles of a shrinking domestic market, Japan remains committed to quality and has continuously invested in cutting-edge technologies.
The United States also plays a crucial role, with its production capacity often fluctuating in response to economic shifts. Investments in modernization and technological integration have been essential for steel plants across America. As domestic demand rises, especially in construction and automotive sectors, the U.S. focuses on producing specialized steels for national consumption and international trade.
Russia, with its vast natural resources, stands as a significant player in the steel industry. The nation's strategic location allows it to supply both European and Asian markets efficiently. Innovations in production technology and efforts to improve environmental standards have strengthened Russia's position in this space. Collaborations with global companies further enhance its production capabilities, making Russian steel a fierce competitor on the international stage.
"Steel is the cornerstone of our industrial fabric, a material that shapes contemporary life and propels economies forward," notes an industry expert from the World Steel Association, highlighting the significance of these nations’ contributions to the global market.
Each of these countries uniquely influences the global stage, creating a competitive yet collaborative landscape. As they push the boundaries of production capabilities and sustainability, it becomes evident how integral these nations are to the structure and future of the global steel industry. The interplay between tradition and innovation in these countries ensures that steel remains a vital component of infrastructural development worldwide.
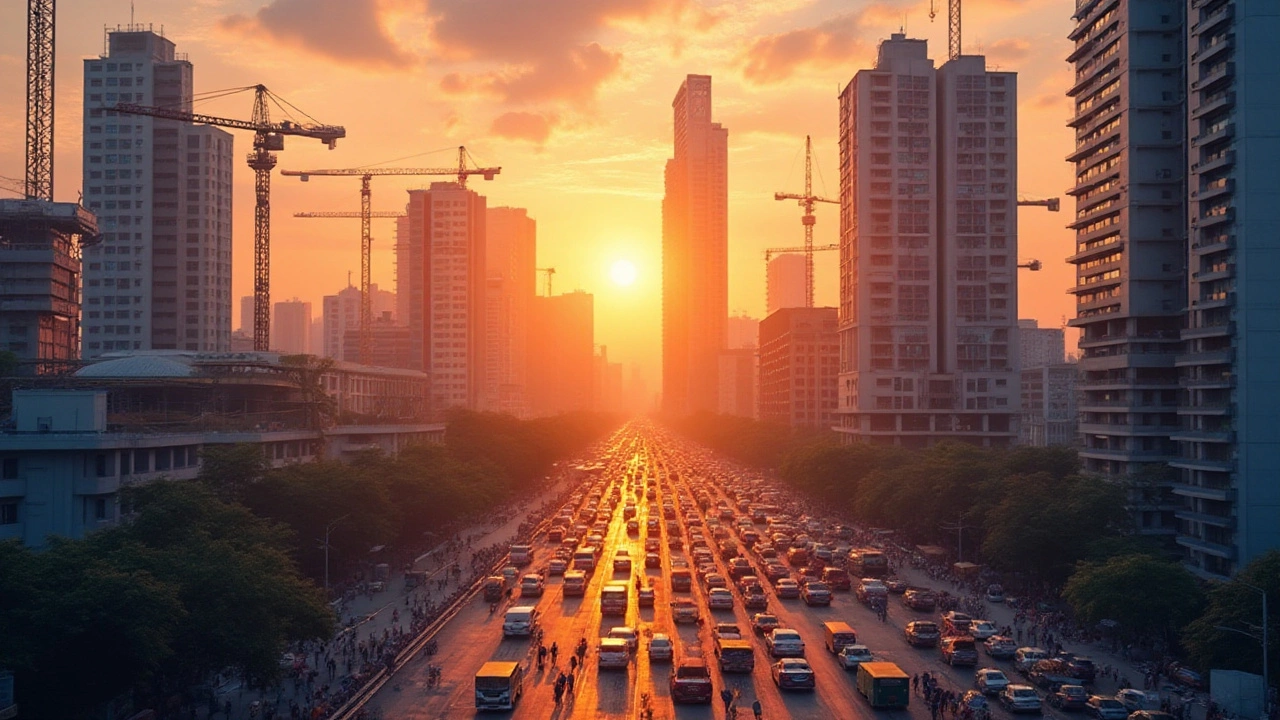
Leading Steel Manufacturing Companies
In the world of steel, giants reign supreme, spearheading innovation while sustaining massive production capacities. These companies not only define trends but also set the pace for technological advancements and environmental norms. At the heart of the global steel industry are corporations with the power and capacity to influence markets worldwide. One often starts with ArcelorMittal, a titan that stands unparalleled in its global reach. Headquartered in Luxembourg, ArcelorMittal has a staggering ability to adapt, diversify, and innovate. They don’t just focus on quantity but refine quality, ensuring that their steel products cater to diverse industries ranging from automotive to construction. This multifaceted approach has been their key to erasing borders and serving nearly every corner of the globe.
Then, there’s China's Baowu Steel Group, a name that's not just a leader in Asia but also a formidable presence globally. Such a position showcases their strategic prowess in scaling their operations post-merger with Wuhan Iron and Steel. Baowu's narrative is tightly interwoven with innovation—constantly investing in newer technologies to make their processes more efficient. The company’s commitment is reflected in its R&D divisions, which channel efforts towards sustainable and environmentally friendly production techniques. Their emphasis on green steel initiatives places them at the forefront of the sector's climate-conscious future.
"Forging a sustainable future: our path forward involves blending innovation with responsibility," states a Baowu executive, underpinning the company's vision.
Nippon Steel of Japan also holds its ground strongly among these leaders, with roots that run deep into history. They are known for their technological edge—often leading the charge with cutting-edge research and innovative solutions. This company's dedication to improving product strength and versatility has made them a partner of choice for automotive and infrastructure projects massive in scale. Not one to rest on past laurels, Nippon Steel has embarked on ambitious goals to reduce its carbon footprint, thereby aligning its mission with global sustainability challenges.
If you dive deeper into the demographics of steel production, Posco from South Korea emerges as a leader driven by relentless innovation. Posco's operations are a testament to efficient infrastructures and forward-thinking strategies that champion cost-effectiveness without compromising quality. Their integrated mills are a fine example of what cutting-edge technology can achieve when sustainability is on the agenda. By implementing smart manufacturing systems and investing in cleaner energy sources, Posco shows an unwavering commitment to the future.
This table reflects how these giants compare in recent financial metrics, illuminating their global dominance:
Company | Annual Revenue (2023) | Production Capacity (Million Tonnes) |
---|---|---|
ArcelorMittal | $70 billion | 100 |
Baowu Steel Group | $80 billion | 111 |
Nippon Steel | $50 billion | 55 |
Posco | $60 billion | 42 |
While these companies carry the mantle of established industry leaders, emerging markets are stepping into the spotlight. Countries like India with industry players such as Tata Steel are making strides that could reshape the future map of global steel production. Tata Steel’s innovative projects and ambitious growth plans reflect a promising trajectory. This mélange of established and growing companies tells a larger story about the steel industry—a story where tradition meets transformation, defining an industry critical to modern civilization's advancement.
Technological Innovations
The steel industry has been a bedrock of technological change, with consistent advancements propelling it into the future. The realm of steel manufacturing today isn't what it used to be decades ago, thanks to groundbreaking developments in production processes and material science. These innovations have not only enhanced efficiency but have also brought about significant environmental benefits.
One of the most notable technological strides is in the area of automation and digitalization. Manufacturing plants worldwide are increasingly adopting smart systems and internet-of-things (IoT) technologies. This transformation is allowing factories to monitor production processes in real-time, minimize waste, and improve the overall quality of the steel produced. With advanced sensors and data analytics, these smart factories are a glimpse into manufacturing’s futuristic visage.
"The integration of AI and robotics into steel-making will revolutionize the industry, much like how the McKinsey report highlights unprecedented efficiency gains in other sectors," said a technology analyst during a recent seminar.
Another significant advancement is in energy optimization. The push towards greener technologies has led to the rise of electric arc furnaces, which use electrical energy rather than carbon-intensive blast furnaces. This transition is not only reducing carbon footprints but also cutting costs in energy consumption. With many countries committing to net-zero emissions, innovations like these become vital for a sustainable future.
3D printing in steel production is yet another rising star. By leveraging additive manufacturing techniques, companies can now produce complex steel components with unprecedented precision and minimal material wastage. This technology is especially beneficial in industries that need customized solutions or are dealing with structures exposed to severe stresses, such as aerospace and automotive sectors.
In terms of material improvements, high-strength, lightweight steels are the buzz. The development of these materials is key to applications in automotive and construction industries where durability meets efficiency. Manufacturers are actively engaged in research to find the perfect balance, and these efforts have already led to steels that are significantly lighter yet offer superior strength.Global steel production is indeed on the cusp of a transformative era, with technology playing the pivot. As we look to the horizon, breakthroughs in hydrogen-based steel production technology are particularly promising, proposing a near-zero-emissions alternative to traditional methods.
The journey of technological renewal in the steel industry is just beginning, suggesting a tantalizing future replete with innovation. This evolution signifies not just an enhancement in production but also a commitment to an eco-friendly industrial future. The world is watching; each new development shapes the structures of tomorrow.
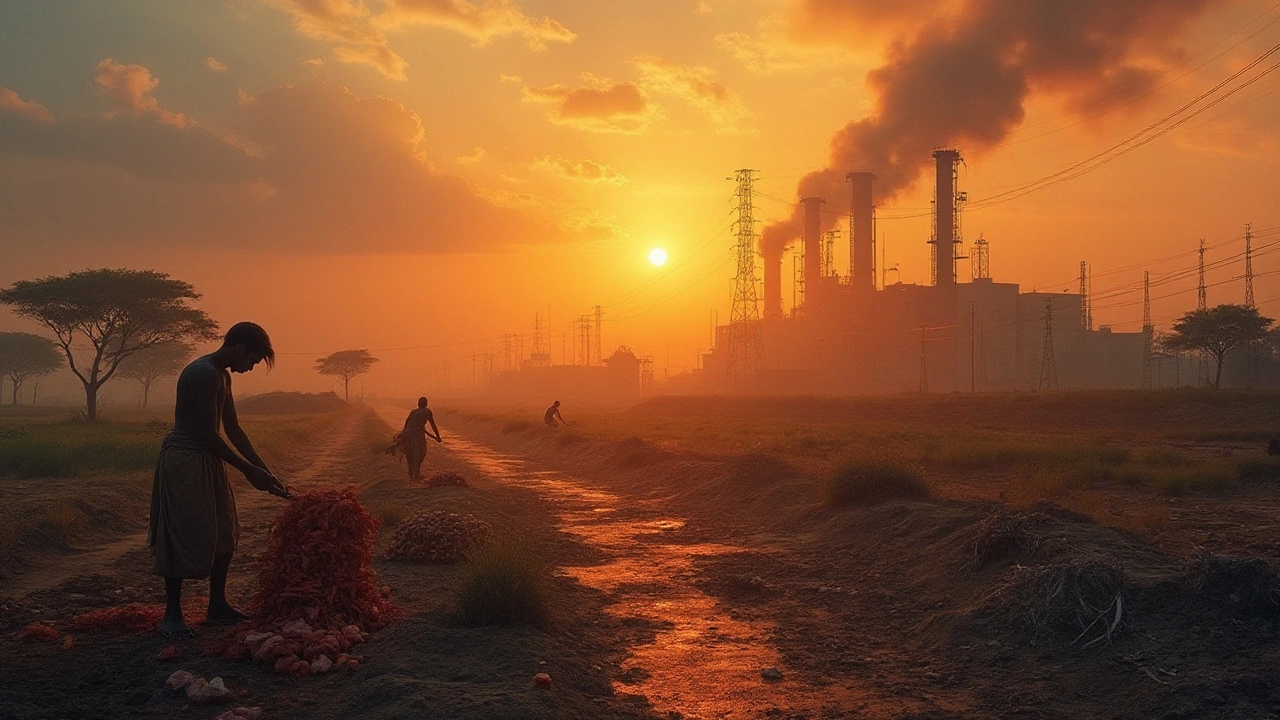
Environmental Impact and Sustainability
The steel industry has long been a cornerstone of industrial progress, but its environmental footprint is a towering concern. By nature, the production of steel is energy-intensive and contributes significantly to carbon emissions, necessitating urgent calls for greener solutions. Steel plants are among the most significant industrial polluters, with reports suggesting the industry accounts for about 8% of the total global CO2 emissions. This reality pushes manufacturers to rethink processes and seek sustainable alternatives for future ingenuity. Such challenges give rise to an array of innovative strategies aimed at reducing the carbon footprint of steel production.
At the forefront of this endeavor is the adoption of hydrogen as a replacement for carbon in the iron ore reduction process, a practice that offers the tantalizing possibility of zero-carbon steel. Hydrogen-based reduction technologies, while still in developmental stages, signal a transformative shift toward eco-friendly production methods. Coupled with advancements like carbon capture and storage (CCS), the industry is mapping out a roadmap toward achieving cleaner production practices. Despite these strides, the transition is marred by technological, financial, and infrastructural hurdles that require collective effort and substantial investment.
Leading the path in environmentally sustainable manufacturing are countries like Sweden and Germany, where initiatives such as the HYBRIT project in Sweden aim to revolutionize steel manufacturing. The project proposes using fossil-free electricity and green hydrogen, potentially eliminating virtually all emissions. This innovative method has the power to stir a sizable reduction in the global emission tally, underscoring the crucial role of technological innovation in driving the sector's future. Meanwhile, Germany’s SALCOS project sees decarbonization as a two-prong approach, combining hydrogen and renewable electricity to produce steel sustainably.
Stakeholders across the steel value chain are increasingly acknowledging their role in fostering environmentally responsible practices. The push towards recycling is a notable shift, with the industry already making use of scrap reserves to reduce dependence on virgin raw materials. Recycling steel not only conserves natural resources but also utilizes significantly less energy, slashing emissions down by about 60%.
"The steel industry must adopt a circular economy mindset, maximizing recyclability while minimizing waste and emissions," said Fatih Birol, Executive Director of the International Energy Agency.As companies work towards creating a sustainable loop in steel production, supporting policies, and collaborations become increasingly vital.
Yet the road ahead is laden with complexities. While innovations promise a greener future, questions about cost-feasibility remain. The widespread availability and affordability of cleaner steel remain hurdles, as does consumer acceptance and regulatory pressures. Importantly, as global steel production grows, emerging markets are compelled to balance developmental aspirations with environmental stewardship, fueling a broader dialogue across continents on how to synergize progress with responsibility.
Looking ahead, the marriage of sustainability and technological advancements offers a vital avenue for the steel industry to realize its potential as a leader in the green industrial revolution. The stakes are high, with a global community watching closely, hoping for an industry transformation that aligns resilience with positive environmental impact. As industry players continue this shared journey, their adaptability to embrace sustainable practices will determine both their competitive edge and their contribution to a greener planet.
Future Trends in the Steel Industry
As the globe strides forward into a new era of industrial development, the steel industry stands on the cusp of transformative change. With technological leaps, increased environmental awareness, and shifting market dynamics, the next decade is anticipated to shape steel like never before. A pivotal trend to watch is the innovation in production processes that promise greater efficiency and reduced carbon footprints. Global steel production is gradually embracing green technologies, from harnessing solar power in steel plants to employing hydrogen-based methods instead of traditional coal for iron smelting. The implementation of these emergent technologies is forecasted to substantially drive down emissions, marking a climate-conscious shift for the industry.
Moreover, the landscape of steel manufacturing is being redefined by digitalization. Smart technologies are now integral to operations, improving everything from predictive maintenance to supply chain logistics. Artificial intelligence and machine learning are being leveraged to refine fabrication techniques and optimize resource use, enhancing production quality while minimizing waste. We see manufacturers racing to adopt IoT solutions to automate processes, ensuring precision, boosting output, and lowering costs. Interestingly, this drive towards Industry 4.0 in steel is not just about efficiency; it's about resilience. By adopting these digital tools, steel producers can better navigate the uncertainties of global markets.
The geopolitical arena also influences the future of steel. Economic policies, trade tariffs, and international collaborations heavily sway production and distribution. Countries like China and India continue to assert themselves as leaders in steel manufacturing, thanks to their vast natural resources and expanding industrial bases. There's potential for them, along with emerging markets, to shape the competitive landscape, stirring both cooperation and competition globally.
The World Steel Association has predicted, "The demand for innovative, sustainable steel solutions is on the rise, driven by a pressing need for ecological responsibility." This foresight emphasizes the growing market for steel that not only meets structural needs but also aligns with sustainable practices.
In synch with this sustainability push, recycling is becoming a central pillar of steel production practices. The cyclical nature of steel — its ability to be melted down and repurposed repeatedly without losing strength — positions it as an environmentally friendly material choice. As industries and consumers pivot towards greener practices, steel’s recyclability ensures its continued relevance.
In contemplating the future, it's critical to consider advancements in alloy development too. High-strength, lightweight steels are emerging as the material of choice in sectors like automotive and aerospace, where efficiency and performance are paramount. This trend isn't just a technical evolution; it represents a strategic adaptation to meet the changing demands of a rapidly modernizing world.
Finally, as the steel industry pushes towards a futuristic horizon, education, and skill development will play central roles. Equipping the workforce with the knowledge and expertise needed to operate new technologies and adopt innovative practices will ensure a robust transition into the next chapter of steel production. Thus, the future of this industry is not just in the hands of breakthrough innovations or strategic trade policies but lies equally in investing in human capital.
Therefore, tracing these threads of innovation, digitalization, geopolitics, and sustainability, we get a tapestry of a future that promises to keep steel at the core of global infrastructure — resilient, adaptable, and green. As we edge closer to this future, these trends demonstrate the steel industry’s readiness to adapt, evolve and thrive in an ever-changing global landscape.