Thinking about starting a small manufacturing business? You're probably wondering just how much cash you need to get off the ground. It's a puzzle many people face, but don't worry—it's not as daunting as it seems.
First off, identifying the initial expenses is crucial. These include everything from equipment and raw materials to rent and utilities. You might be surprised to learn that these costs can vary a lot depending on what you're aiming to manufacture. But here's a fascinating tidbit: many entrepreneurs find that equipment often takes the largest chunk of their budget.
It's vital to know what tools and machines are essential for your specific line of production. Whether it's a simple hand tool or a more complex machine, each piece adds up. Researching what you absolutely need versus what would be nice to have can help in keeping costs in check.
- Understanding Initial Expenses
- Essential Equipment and Tools
- Budgeting for Space and Utilities
- Cutting Costs and Strategic Planning
Understanding Initial Expenses
Kicking off a small scale business isn't just about having a great idea—it's about understanding the costs involved right from the start. If you're venturing into manufacturing, these initial expenses can be the make-or-break factor.
Essential Costs to Consider
First up, you've got to think about raw materials. Depending on what you're manufacturing, raw materials can take up a considerable part of your budget. Getting these on hand ensures you're ready for production from day one.
Next, let’s talk equipment. For many manufacturing startups, this is where a big chunk of the money goes. If you’re making something like handmade soaps, your equipment needs will be minimal—mixers, molds, stuff like that. But, say you're getting into 3D printing, you might need pricier machines. Estimate carefully, don’t just buy shiny new stuff you don't need.
Rent and Utilities
Don't overlook the cost of space. Whether it's renting an industrial unit or setting aside a corner of your garage, there's likely a cost attached. And don't forget utilities—electricity and water bills will be part of your regular outgoings, especially in any production process that uses a lot of energy.
Did you know? On average, 30-40% of manufacturing costs are from utilities alone. It's a hidden expense that startups often underestimate.
Legal and Administrative Fees
And then, consider the less exciting stuff—permits, licenses, and insurance. These are non-negotiable for any business, including a small scale business. We all have to face the paperwork—account for this in your budget and avoid any slugging legal fines or delays.
- Business registration fees
- Legal licenses specific to your industry
- Insurance policies
The goal is to have a solid understanding of these expenses from the start so you’re not caught off guard down the road. Clear planning keeps the wheels turning smoothly as you start to build your business empire!
Essential Equipment and Tools
Getting the right equipment is one of the main steps in setting up your manufacturing startup. Let's break it down to help you know where to start and what to budget for.
Identifying Your Needs
Before buying anything, you need to figure out what's essential. The equipment you need depends heavily on what you plan to manufacture. For instance, if you're diving into textile production, sewing machines might be at the top of your list. But, if you're creating metal parts, you might need cutting and milling machines.
New vs. Used Equipment
Should you buy shiny new machines or look for used ones to save some cash? It depends on your budget and timeline. New machines offer the latest technology and warranties, but they're costly. Used equipment can save you loads, but make sure they are well-maintained. Some startups cut expenses by leasing equipment until they have a steadier cash flow.
General Equipment Costs
Here's some rough numbers to keep in mind:
- Sewing Machine: Costs for new models start around $200, but heavy-duty variants can cost several thousand.
- 3D Printers: Small scale versions begin at $300, while industrial quality options reach $5,000 or more.
- CNC Machines: Prices vary widely from $2,000 to upwards of $100,000, depending on capabilities.
There's often financing available for expensive machinery. Check with local banks and financial institutions that cater to small scale business ventures.
Additional Tools
Don’t forget about the small stuff. Hand tools, measuring devices, and safety gear are necessary. While they might not break the bank, these costs can add up quickly. Budgeting a few hundred dollars for miscellaneous tools and equipment is a smart move.
Investing in the right equipment and tools sets the foundation for a smooth-running manufacturing business. It’s all about balancing quality and cost while making sure you have everything you need to start producing your product effectively.
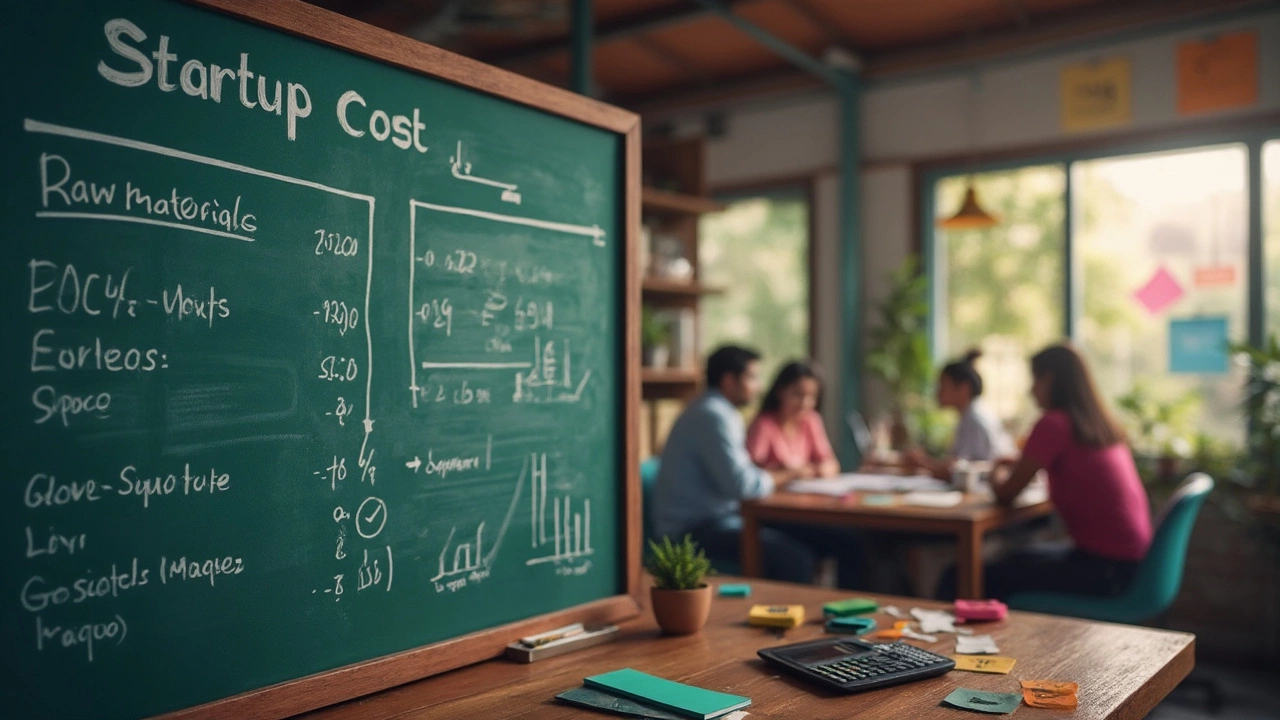
Budgeting for Space and Utilities
Getting the right space for your manufacturing startup is no small task. Whether you're renting a facility, setting up in a shared space, or even building from scratch, the costs can add up quickly. Let's break it down to make this seemingly monumental task a little less intimidating.
Finding the Right Space
Your manufacturing business's location can impact everything from distribution to employee satisfaction. Do you need a heavily industrial region, or can you work in a more mixed-use area? Proximity to suppliers and customers can save both time and money on logistics.
Rental costs for industrial spaces can vary wildly depending on your city, so it's worth looking into areas with lower overheads if budget is tight. An interesting tip: some budding entrepreneurs have found repurposed spaces like old warehouses or even large garages which can be converted into effective workspaces.
Breaking Down Utility Costs
Utilities are another key aspect of your monthly budget. When you're running machines, electricity costs are significant. On average, US small manufacturers spend around $1.47 per square foot on electricity annually. You'll also need to budget for water, especially if your production involves cooling processes or other heavy uses. Don’t forget about waste disposal, which might include special arrangements depending on your materials.
Cost-Saving Tips
There are ways you can cut corners without sacrificing quality or efficiency:
- Consider energy-efficient equipment and lighting to save on electricity costs.
- Look into grants or incentives for businesses that adopt sustainable practices.
- Track utility usage regularly and identify patterns to find areas for improvement.
Utility | Average Cost per Month |
---|---|
Electricity | $200 - $500 |
Water | $50 - $150 |
Disposal | $30 - $100 |
Remember, proper planning and a keen eye for opportunities can make managing space and utility costs much simpler. By optimizing these expenses, you can free up resources to invest in other crucial areas of your small scale business.
Cutting Costs and Strategic Planning
Starting a small scale business doesn't mean you have to spend big bucks. In fact, smart strategic planning can make a world of difference. So how can you save money while making sure your manufacturing startup hits the ground running?
Lease, Don't Buy
The first tip is to consider leasing equipment rather than buying it outright. This approach not only reduces initial expenses but also offers flexibility to upgrade as your business grows. Plus, it ties up less capital, which is crucial when you're just getting started.
Optimize Your Space
Space can be a considerable chunk of your budget. Instead of splurging on a large facility, think about starting small. A shared workspace or a smaller rental can cut costs significantly. There's no need to go grand when your needs might not demand it yet.
Hire Smart
People are essential, but salaries can add up quickly. Hiring part-time employees or freelancers can help manage labor costs effectively in the beginning. With this approach, you can get the skills you need without a full-time financial commitment.
Source Materials Locally
When it comes to raw materials, local sourcing can often bring costs down while also reducing shipping fees. Plus, you'll likely get your materials faster, which can streamline production.
Energy Efficiency
Operational costs are another area to scrutinize. Investing in energy-efficient machinery might seem costly upfront, but the long-term savings on utilities can be significant. Simple adjustments like energy-saving bulbs and appliances can also contribute to cost reduction.
Expense Area | Cost-Saving Potential (Annually) |
---|---|
Leasing Equipment | $5,000 |
Optimizing Space | $3,000 |
Hiring Strategy | $4,500 |
Local Sourcing | $2,500 |
Energy Efficiency | $2,000 |
These strategic choices illustrate how focusing on manufacturing startup costs can help set a strong foundation for your business. Thinking creatively about cost-cutting can help your venture not just survive, but thrive.