The landscape of steel manufacturing in the United States is a fascinating subject, steeped in history and innovation. It's a crucial part of the nation's industrial fabric and has played a significant role in shaping its economy. Knowing the distinguished names in this industry adds a layer of appreciation for the steel used in countless applications around us, from towering skyscrapers to finely crafted automobiles.
In recent decades, US steel manufacturers have faced numerous challenges, from international competition to technological advancements. Yet, several stand out as stalwarts of quality and efficiency. These leaders have not only preserved but have innovated, creating products that are pivotal to infrastructure and industry.
With each steel company's story, we step into a world where tradition meets cutting-edge technology, ensuring that the US remains a powerhouse in global steel production. Embark on a journey that explores the scale and scope of these impressive operations and the economic ripples they create across the country.
- A Glimpse into America's Steel Industry
- The Rise of Steel Giants
- Innovations and Technology in Steel Production
- Profiles of Top US Steel Mills
- Economic Impact and Employment Opportunities
- Future of Steel Manufacturing in the US
A Glimpse into America's Steel Industry
At the heart of America’s industrial prowess, the steel industry stands as a pillar of strength and resilience. The journey of steel in the United States began in the late 19th and early 20th centuries, recognized as a transformative period marked by technological advancements and significant economic shifts. The post-Civil War era spurred rapid industrialization, witnessing the rise of formidable entities like Carnegie Steel Company. This progression laid the foundation for what would become a vast network of steel production, crucial to the country’s infrastructure and economic growth.
The importance of steel extends beyond its functionality; it is a symbol of progress and ingenuity. Over the decades, the industry has evolved, facing challenges like volatile pricing and environmental regulations. Yet, steel manufacturers in the US remain innovative, focusing on sustainable practices and advanced technology. The American steel industry prides itself on producing an impressive range of steel products used in various sectors, including construction, automotive, and aerospace. A significant portion of this innovation is credited to the integration of modern technologies like AI and IoT in manufacturing processes, improving efficiency and sustainability.
A fascinating aspect of the industry's landscape is the regional diversity of steel manufacturing plants. From the iconic mills in Pennsylvania and Ohio to burgeoning facilities in the southern and western states, each region contributes uniquely to the industry’s fabric. This geographic spread not only underscores the versatility of American steel production but also highlights the vital economic contributions made by these plants to local communities. Interestingly, the steel industry supports over 140,000 jobs directly, while indirectly facilitating employment for more than a million people across the country.
The US steel industry's allure extends globally, where it competes on the international stage. In recent years, exports have witnessed a steady growth, reinforcing the country’s standing as a global state of the art manufacturer. Yet, this hasn’t come without its challenges. Tariffs and international trade dynamics often play significant roles, influencing both production and pricing strategies. As policies shift, the American steel industry must adapt, maintaining competitiveness while adhering to stringent quality standards.
"The steel industry remains vital to the American economy, embodying both our industrial past and a sustainable future," remarked industry analyst Dominic Barton, encapsulating the essence of its enduring legacy.
Today, the focus is as much on future potential as it is on present capabilities. Initiatives to integrate more sustainable practices are underway, with older plants retrofitting to meet greener standards, and new facilities built with a focus on environmental stewardship. This aligns with the broader industry trends towards decarbonization, setting new benchmarks for global steel manufacturing standards, and assuring a greener, more efficient future for the industry.
The Rise of Steel Giants
The development of the steel industry in the United States and the emergence of its giants trace back to a pivotal era in American history. The late 19th and early 20th centuries marked the dawn of industry and innovation, with steel leading the charge. Industrial magnates like Andrew Carnegie recognized the transformative power of this robust material, paving the way for an age of unprecedented growth. In this period, regions like Pittsburgh, often dubbed the “Steel City,” became synonymous with the burgeoning industry, attracting millions of workers and helping to shape America’s urban landscape. The U.S. steel manufacturing sector grew at an astounding rate, driven by rapid industrialization and expanding rail networks, which created a massive demand for steel rails.
During this era, large-scale manufacturing plants were established, many of which still stand today, representing landmarks of the American industrial age. Factories employed thousands, and communities sprang up around them, thriving on the economic opportunities these steel mills provided. The industry wasn’t without its rivals, as competition from Europe, particularly from Britain and Germany, was fierce. However, American ingenuity and the vast natural resources available gave the U.S. an edge that would serve it well into the 20th century. The creation of major corporations cemented the United States as a formidable player on the global steel stage.
The evolution of technology played a crucial role, yet it was bolstered by strategic mergers and innovations. The introduction of the Bessemer process, for example, revolutionized steel production by significantly reducing the cost and time required to produce steel, enhancing the competitive capacity of American mills. This transformation enabled the mass production of steel and fueled growing industries such as construction and transportation. As cities expanded, so did the influence of steel, which became the backbone of America’s infrastructure. Steel mills became synonymous with progress and prosperity, symbolizing the country’s ascent to industrial preeminacy.
The cry for innovation didn't stop there. As the 20th century advanced, emerging technologies and processes—such as the basic oxygen method—further refined production techniques. This helped U.S. mills maintain their status at the forefront of the industry. An iconic era of the 1950s and 1960s saw the rise of integrated mills, which combined all processes from raw materials to finished products. These giants covered vast areas and employed thousands, laying the groundwork for future growth. However, the industry had to continuously innovate to remain competitive amidst global pressures and the advent of cheaper overseas labor. The strength of these steel giants wasn't just in their manufacturing prowess but also in their ability to adapt and scale operations in response to changing global market dynamics.
"The strength of the steel industry is not just in its past, steeped in tradition and history, but in its ability to innovate and adapt to the future," noted industry expert and historian, John Peterson, in his reflective work on industrial evolution.
Into the late 20th century and beyond, the rise of mini mills and the introduction of electric arc furnaces challenged traditional giants but also spurred further innovation. These mills utilized scrap metal and required less investment, making steel more accessible and environmentally friendly. The major steel players adapted by incorporating these practices, ensuring they stayed relevant. Today, the U.S. steel industry is a blend of storied tradition and cutting-edge innovation, thanks to the rise and adaptation of its historical giants.
Innovations and Technology in Steel Production
The steel industry, a cornerstone of industrial advancement, has always been at the forefront of technological innovation. From the Bessemer process of the past to today's cutting-edge methodologies, the evolution has been monumental. One of the most significant modern advancements is the integration of artificial intelligence and machine learning into steel production. These technologies allow for precision that was once unimaginable, optimizing every step of the manufacturing process, from the raw material stage to the final product. By analyzing vast amounts of data, AI systems can predict equipment malfunctions before they occur, thus minimizing downtime and increasing efficiency.
Another leap forward has been the development of new steel alloys. These alloys are engineered to meet specific industry requirements, offering improved performance characteristics such as increased strength, reduced weight, and higher corrosion resistance. Innovations in materials engineering have paved the way for advancements in sectors like aerospace, automotive, and construction. A strong emphasis is placed on sustainability, with new processes aimed at reducing the carbon footprint of steel production. Technologies like electric arc furnaces and basic oxygen furnaces have been optimized to consume less energy, thus playing a vital role in environmentally friendly manufacturing.
The implementation of Industry 4.0 is another marvel of innovation in the steel sector. Utilizing smart factory principles, steel manufacturers can achieve unprecedented levels of productivity and quality. Through sensors and the Internet of Things (IoT), every aspect of production is monitored in real-time, allowing for instant data-driven decision-making. This extensive connectivity also enables predictive maintenance, whereby potential faults are identified and rectified before any disruption to production occurs. As Forbes noted, "The steel industry, driven by global competition, is in the midst of a digital transformation that will revolutionize its operational norms."
Recycling technology in steel manufacturing has also seen remarkable progress. Modern methods can recycle steel with virtually no loss in quality, which has enormous environmental and economic benefits. Steel is unique in its ability to be recycled countless times, contributing to the circular economy. In recent years, advancements in sorting and processing technologies have enhanced the efficiency and purity of recycled materials, making them as desirable as primary materials. The process involves sophisticated separation techniques, allowing manufacturers to reclaim nearly 100% of steel content from end-of-life products. This not only prevents waste but reduces the demand for raw resources, which is a critical step toward sustainable industrial practice.
Automation has also considerably influenced the steel manufacturing landscape. Robotic systems are increasingly employed for tasks that require high precision or pose risks to human workers. From raw material handling to the finishing processes, robotics accomplish tasks with consistent accuracy, reducing the margin for error significantly. These systems are continually improved to adapt to different manufacturing needs, offering flexible solutions for the production line. This adaptability is showcased in new robot models capable of performing multiple tasks, enhancing the versatility and efficiency of manufacturing environments.
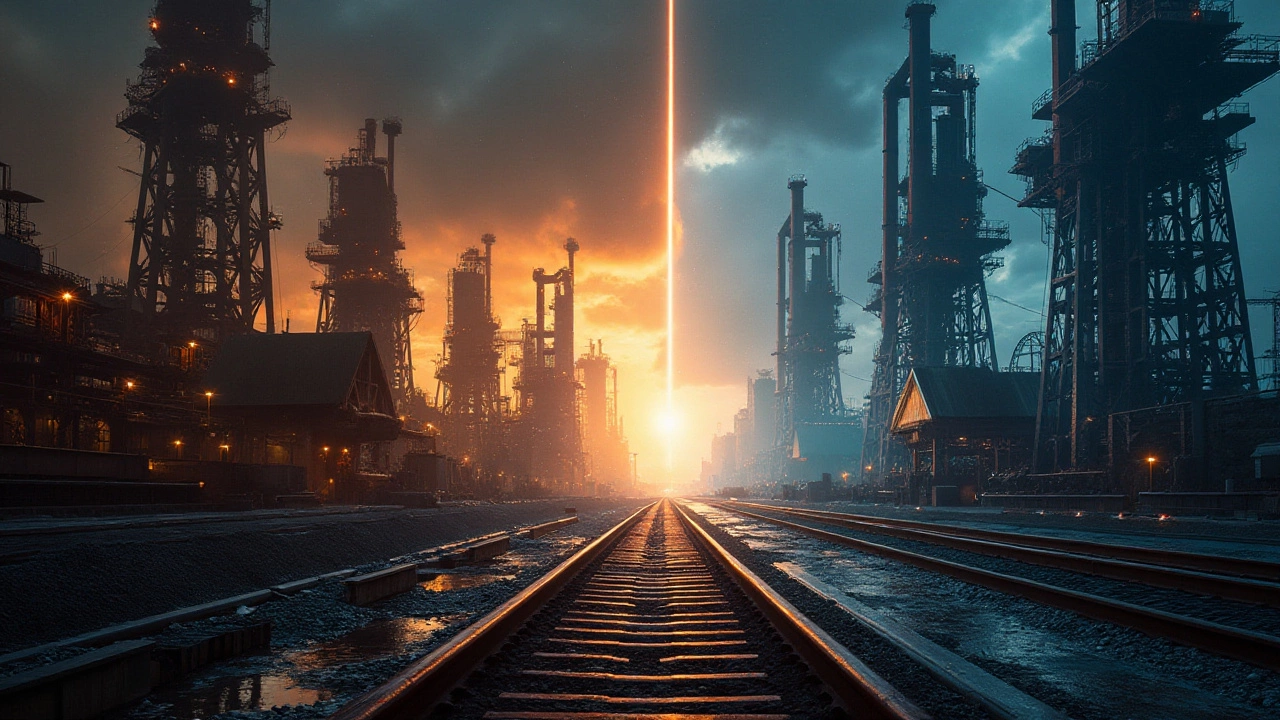
Profiles of Top US Steel Mills
The United States is home to several noteworthy steel mill giants that continue to shape the industry's trajectory with their innovative and efficient operations. Among them, Nucor Corporation stands as a prominent leader, often hailed as a trailblazer due to its agile practices and innovative strategies. Founded in 1940, Nucor's rise to prominence was marked by its evolution into a key player in the US steel manufacturing landscape. Known for its mini-mill model, embracing electric arc furnace technology, Nucor redefined production processes by eschewing blast furnace methods. With a commitment to sustainability, the corporation not only excels in producing high-quality steel but also emphasizes recycling, with the majority of their steel coming from recycled scrap. The company's guiding ethos speaks volumes: "During downturns and upturns, you need to stay focused on doing things right," states former Nucor CEO, John Ferriola in an industry interview, highlighting the importance of consistent quality and strategic foresight.
Another formidable presence in the American steel arena is United States Steel Corporation, commonly known as U.S. Steel. Established in 1901, it's one of the largest integrated steel producers, making an indelible mark with its vertically integrated approach. This methodology allows U.S. Steel to control every step of the production process, from mining raw materials to creating finished goods, ensuring exceptional quality. As environmental concerns grow, the company has been pushing towards low-emission methods, investing in technologies to facilitate cleaner production processes. Their commitment doesn't end there. With over 20 million tons of production capacity annually, U.S. Steel not only fulfills domestic needs but also secures a significant position in the international market. The company's impact on creating employment and bolstering local economies is substantial, with operations sprawling across numerous states, thus reinforcing its influence in the industry.
Navigating The Modern Challenges
In navigating today's economic landscape, AK Steel, now part of Cleveland-Cliffs Inc., represents a blend of tradition and modernity. Founded in the late 19th century, AK Steel has consistently demonstrated resilience, seamlessly incorporating new technologies while respecting its foundational roots. Known primarily for producing flat-rolled steel, its specialty lies in automotive steel, thanks to advanced coating lines that provide corrosion-resistant products essential for vehicle manufacturing. This adaptability is critical, especially in an era where automobiles are transitioning to lighter structures and more durable materials. Cleveland-Cliffs, leveraging AK Steel's strengths, now commands a unique position in the industry by merging steel production with raw material supply chains, thereby achieving unprecedented streamlining in operations.
To gauge the lasting impact of these steel titans, it's essential to appreciate their contribution to regional economies and the lengths at which they go to ensure sustainability and innovation. A comparison of production capacities and initiatives often reveals more than simple statistics. Consider that Nucor alone produces over 27 million tons annually, underscoring its standing as the largest steel producer in the nation, a title achieved through relentless pursuit of excellence and strategic plant acquisitions. Identifying such key players isn't merely about understanding their past achievements but spotting their potential in propelling the U.S. steel industry into new horizons marked by technological triumphs and sustainable practices.
Economic Impact and Employment Opportunities
The steel manufacturing industry is more than just a pivotal sector; it's a backbone that supports a substantial number of livelihoods and fuels economic growth in the United States. The industry's economic impact is profound, as it weaves its influence into various sectors like construction, automotive, and machinery. Every segment of modern life, from public transit systems to appliances at home, is intertwined with steel, highlighting its indispensable role. Due to its foundational nature, the steel industry not only helps build cities but also contributes significantly to the gross domestic product and regional economies.
The employment opportunities within the US steel mills are vast and multifaceted. From jobs that require high-level engineering expertise to those that need skilled laborers in production lines and maintenance crews, the industry offers a wide spectrum of careers. A factory floor is a dynamic place where innovation meshes with time-honored procedures, offering hands-on learning opportunities. In cities with significant steel manufacturing presence, the mills often become a critical component of local employment strategies, attracting talent and retaining the workforce with competitive salaries and benefits.
Due to technology-driven changes, the industry also demands roles in data analysis, environmental compliance, and engineering solutions. As these cutting-edge technologies get implemented, they translate into better efficiencies and new job types, showcasing how the sector is both a keeper of tradition and a harbinger of innovation. According to a recent industry report, the strategic implementation of automation and AI technologies has created an upward trend in technical job opportunities, offering promising prospects for those entering the field.
"The steel industry is not just making materials; we are building the literal framework for innovation," says Mike Rippey, CEO of a leading US steel manufacturing company.
The steel mills' economic contribution extends beyond direct employment. They invigorate local businesses, from suppliers and transport services to cafes and shops frequented by workers. The symbiotic relationship between mills and their towns allows for community growth, creating a micro-economy that allows smaller enterprises to thrive alongside their industrial neighbor. As the steel industry progresses, it also plays a part in financing community projects and sometimes even sponsors educational scholarships to foster new generations of talent.
Educational institutions near industrial hubs often tailor their curriculums, providing specialized training and apprenticeship programs. This collaboration between academic and industrial entities ensures a steady flow of skilled workers, ready to fill in roles demanding expertise and innovation. Notably, efforts are being made to encourage diversity within the workforce, recognizing that a breadth of perspectives contributes to a stronger, more resilient industry.
Key Impact Areas | Details |
---|---|
Sector Influence | Construction, automotive, machinery |
Employment Range | Engineering, production, maintenance |
Tech Integration | Automation, AI, environmental compliance |
In essence, the American steel industry is a dynamic sector wherein each employee plays an integral part in the bigger picture. Its economic ramifications are vast, and its contribution to employment is as diverse as the products it creates. As it continues to transform, the future holds exciting possibilities, driven by both economic demand and a steadfast commitment to innovation.
Future of Steel Manufacturing in the US
Looking ahead, the steel industry in the United States is poised for significant evolution as it navigates the complexities of modern demand and technology. As traditional industries continue to rely on steel, new sectors are emerging with fresh opportunities, pushing the boundaries of steel applications. One of the most promising areas of growth is the incorporation of advanced technologies such as artificial intelligence and machine learning in steel manufacturing processes. These technologies are not only enhancing production efficiency but are also leading to the creation of innovative steel products with superior qualities.
The drive towards sustainable processes is another pivotal trend reshaping the industry's trajectory. As climate change continues to galvanize global efforts in reducing carbon footprints, the steel industry is under pressure to adopt greener, more sustainable practices. This shift isn't merely a trend but rather an urgent call from environmental experts and policymakers alike. By implementing green technologies, like electric arc furnaces and using more recycled steel, the industry is making strides to reduce environmental impact, proving that evolution is both possible and necessary. As noted by the World Steel Association, "The steel industry is prepared to achieve its climate targets by innovating and investing in breakthrough technologies."
Another aspect of the anticipated future involves a stronger focus on the domestic sourcing of raw materials. With global disruptions prompting reconsiderations of supply chains, American steel manufacturers are exploring resilience through localization of resources. This does not merely mean an increase in local job creation but also strengthens economic stability in the long run. Domestically sourced steel feeds into a robust manufacturing sector, which is crucial for national security and infrastructure projects. The change towards greater self-reliance indicates a strategic move to minimize dependence on foreign imports while ensuring consistent quality and pricing within the market.
The skills of the workforce are also evolving in tandem with the technological advancements. As automation and new tech become integral to operations, the need for skilled technicians and engineers is more pronounced than ever. Educational programs and industry-led training initiatives are vital in equipping the next generation with competencies necessary for an advanced manufacturing environment. Community colleges and vocational schools are playing an essential role in this educational renaissance by aligning curricula with industry needs. By fostering a highly skilled workforce, the US steel industry ensures its competitiveness in the global market remains formidable.
In summary, the future of the steel manufacturing industry in the United States is inherently optimistic, driven by a commitment to innovation, sustainability, and resilience. As this sector advances, it remains a crucial component of the nation's economic infrastructure and its path forward. The industry's adaptability and readiness to embrace emerging trends point towards a dynamic evolution that will keep American steel mills at the forefront of global steel production for decades to come.