The world of steel manufacturing has long been dominated by iconic figures who have driven the industry forward with relentless innovation and entrepreneurial spirit. Known affectionately as the 'Kings of Steel,' these industry leaders have left indelible marks on the steel industry.
From shaping the skyline of cities to reinforcing global infrastructures, the contributions of these titans are impossible to ignore. But who are these individuals and companies that have risen to such heights? Their stories are as varied as they are compelling, weaving together tales of ambition, foresight, and technological mastery.
- The Rise of Steel Titans
- Innovations in Steel Production
- Influence and Leadership Within the Industry
- Future of Steel Manufacturing
The Rise of Steel Titans
The advent of the steel industry dates back to the 19th century, a time marked by the unstoppable pace of the Industrial Revolution. It was during this period that the steel industry began to take flight, propelled by visionaries whose influence can still be felt today. The Bessemer process, introduced by Henry Bessemer in 1856, became a groundbreaking method of producing inexpensive steel in large quantities, profoundly impacting the industry. This breakthrough transformed industries and nations alike, as steel quickly became the backbone of infrastructure projects across the globe. Visionary entrepreneurs recognized the massive potential of the industry and seized the opportunity to industrialize steel production.
Andrew Carnegie, a name synonymous with steel manufacturing, emerged as one of these towering figures. Born in Scotland and immigrated to the United States, Carnegie capitalized on innovations like the Bessemer process to build one of the largest steel empires. His company, Carnegie Steel Company, was responsible for building landmarks and infrastructure that powered America’s growth. Carnegie's business practices were revolutionary, prioritizing vertical integration and economies of scale to reduce costs and increase production efficiency. As head of his company, he implemented aggressive strategies, consolidating his power and influence in the industry. By 1901, Carnegie sold his company to J.P. Morgan, resulting in the creation of United States Steel Corporation, the world's first billion-dollar corporation.
The Global Reach and Influence
As demand for steel continued to mount, other nations followed suit in industrializing their own steel production. Around the turn of the century, Germany and the United Kingdom became prominent steel producers. Germany, thanks to the Ruhr Valley’s rich natural resources and state support, became a formidable competitor to the United States in steel production. Friedrich Krupp, another legendary name, established the Krupp company, which played a crucial role in supplying steel for railways, ships, and budding automotive industries. The growth and competitiveness of the European steel market underscored the global nature of the industry and set a precedent for collaboration and competition.
Throughout the 20th century, the industry saw the emergence of new players, notably Japan. After the ruins of World War II, Japan's steel industry rose from the ashes, becoming a cornerstone of its economic prowess. The country’s steel manufacturing prowess is exemplified by Nippon Steel & Sumitomo Metal Corporation, which became one of the largest steel producers in the world. Japan's focus on technological advancement, efficiency, and quality solidified its reputation, making Japanese steel a benchmark for excellence. China, too, entered the scene with a force few can rival, with companies like Baosteel Group Corporation playing significant roles in cementing China's dominance in steel production.
"Steel is the backbone of any modern economy, and as demand for infrastructure grows, so too grows the demand for steel." - John Ferriola, Former Chairman, CEO, and President of Nucor Corporation.
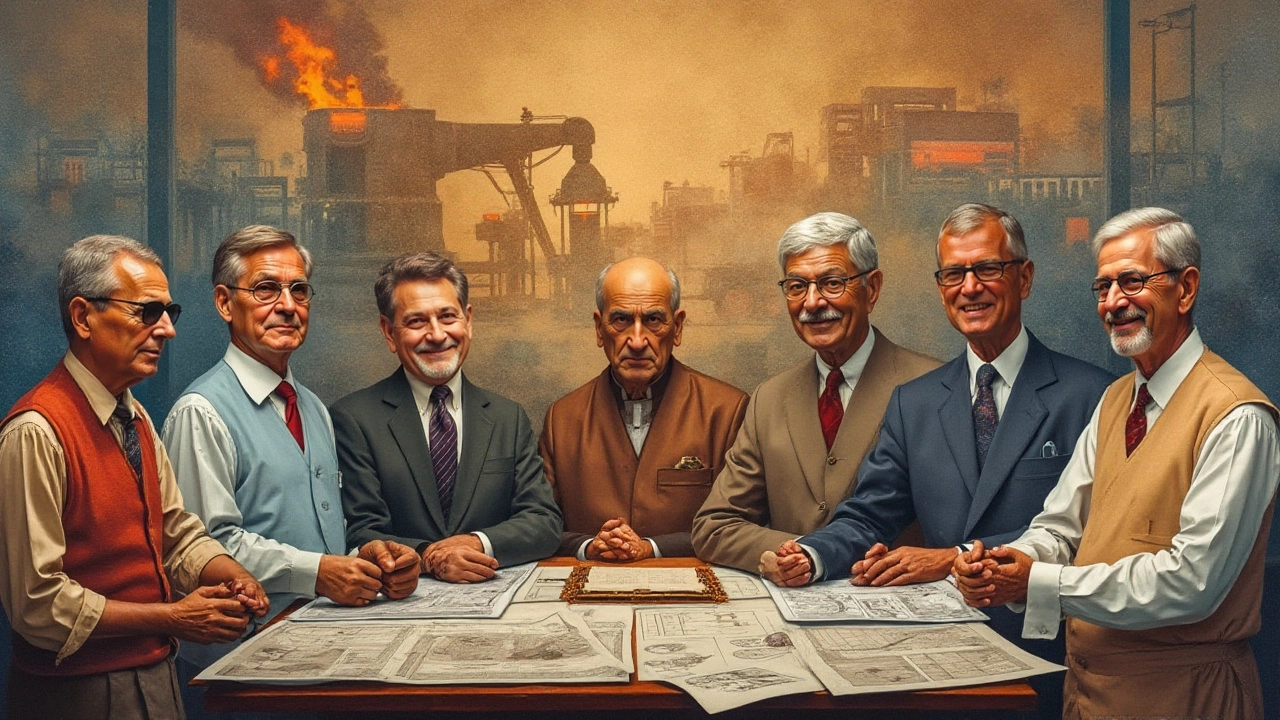
Innovations in Steel Production
Steel production has always been at the cutting edge of industrial innovation, serving as a backbone for countless advancements across sectors. At the heart of these innovations lies a relentless pursuit of efficiency, sustainability, and quality, creating an ever-evolving industry. Take the introduction of the basic oxygen furnace, for example—this technology has drastically reduced processing time while enhancing productivity. It's one of the innovations that showcase the industry's commitment to progress. More recently, electric arc furnaces have garnered attention for their ability to recycle scrap metal, aligning the steel industry with environmental goals. These developments reflect the dynamic nature of steel manufacturing and its response to global challenges.
The push for sustainability in steel production has revolutionized every stage of the process, from raw material extraction to the final product. Companies are investing in cutting-edge technologies like hydrogen-based steelmaking, which promises to virtually eliminate carbon emissions from the process. This approach utilizes green hydrogen instead of coal, marking a significant shift towards greener alternatives. Traditional steelmaking is resource-intensive, but the industry's innovators are determined to change that narrative. Steel giants are actively integrating renewable energy sources like solar and wind into their operations, underscoring their role as leaders in climate-conscious manufacturing. This transformation is as much a response to economic pressures as it is to the growing demands for sustainable practices worldwide.
Now, consider the role of digitalization and automation within steel manufacturing. The integration of artificial intelligence and machine learning has offered a wealth of opportunities for optimization. Advanced modeling systems predict outcomes with remarkable accuracy, reducing waste and increasing efficiency in unprecedented ways. Smart factories, equipped with Internet of Things (IoT) technologies, are revolutionizing how steel plants operate. These automated environments not only enhance productivity but also ensure worker safety by minimizing exposure to hazardous conditions. The digital transformation is reshaping the traditional landscape, helping steel producers maintain their competitive edge in a rapidly changing market.
"Our use of intelligent automation represents a significant leap forward in steel production, enabling us to meet modern demands while remaining environmentally conscious," said Dr. Emily Cheng, a chief innovation officer at a leading steel firm.
Another leap forward in the realm of steel production is the exploration of lightweight steel composites. These materials retain the strength of traditional steel while being easier to manipulate and transport. They are opening new possibilities in sectors ranging from automotive to aerospace, where weight reduction is crucial without compromising durability or safety. Advanced alloys and nano-technological enhancements are enabling engineers to customize steel properties to an extraordinary degree. As a result, steel remains a versatile and indispensable material, positioned firmly at the core of technological progress across industries. Stalwarts of the industry are making bold moves, capitalizing on these innovations to stay relevant and influential.
Here's a glance at some key innovations and their impact on the steel industry:
Innovation | Impact |
---|---|
Electric Arc Furnaces | Enhances recycling capabilities, reduces carbon footprint |
Hydrogen-based Steelmaking | Near-zero emissions; aligns with climate goals |
AI and Machine Learning | Increases operational efficiency; reduces waste |
Lightweight Composites | Offers strength with reduced weight for diverse applications |
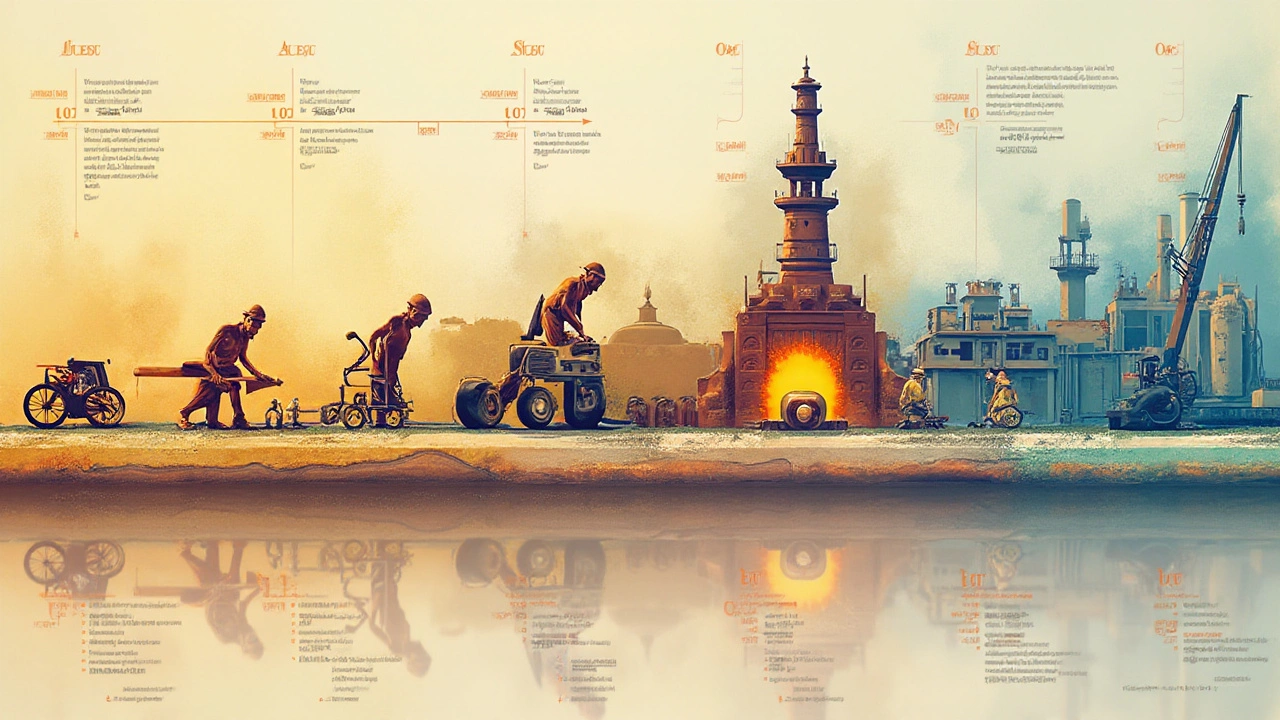
Influence and Leadership Within the Industry
Steel manufacturing has deeply intertwined with global economic growth and technological advancements. As industries evolve, the figures steering these massive enterprises play pivotal roles. These aren't just business magnates, but visionaries who redefine boundaries in steel production by constantly innovating. The most iconic name likely to be mentioned in this context is that of Andrew Carnegie, the 19th-century magnate whose impact is still felt today. His company, Carnegie Steel Company, revolutionized the industry with its strategies and innovations, laying down paths that modern steel manufacturing giants follow.
Their leadership isn't merely about output but about setting benchmarks in sustainability and ethics within the industry. Companies like ArcelorMittal have been at the forefront of integrating eco-friendly processes that significantly reduce carbon emissions. In an industry often criticized for its environmental impact, leadership is defined by those who prioritize greener approaches. Successful leaders inspire by establishing frameworks for a sustainable future, ensuring that the industry doesn’t just chase profits but also considers its global footprint.
"Steel leaders need to be aggressive in adapting to a quickly changing world, but thoughtful of the industries deeply-rooted traditions and responsibilities," said an analyst at World Steel Association.
Industry leaders are also responsible for shaping labor practices. With a workforce running into the thousands, these companies set examples in ensuring fair wages, safe working conditions, and opportunities for upskilling. Tata Steel is known for its pioneering commitment towards employee welfare and community development, setting benchmarks for corporate responsibility.
Leadership extends beyond operations; it's about influence that transcends the boundaries of their corporations, affecting the global landscape and policies. Visionaries like Ratan Tata and Lakshmi Mittal have reshaped not only their own companies but have also influenced global steel industry trends through their strategic decisions. These leaders act as bridges that connect the nuances of local economies with the macroeconomic panorama, ensuring that the steel industry remains robust even amid global challenges.
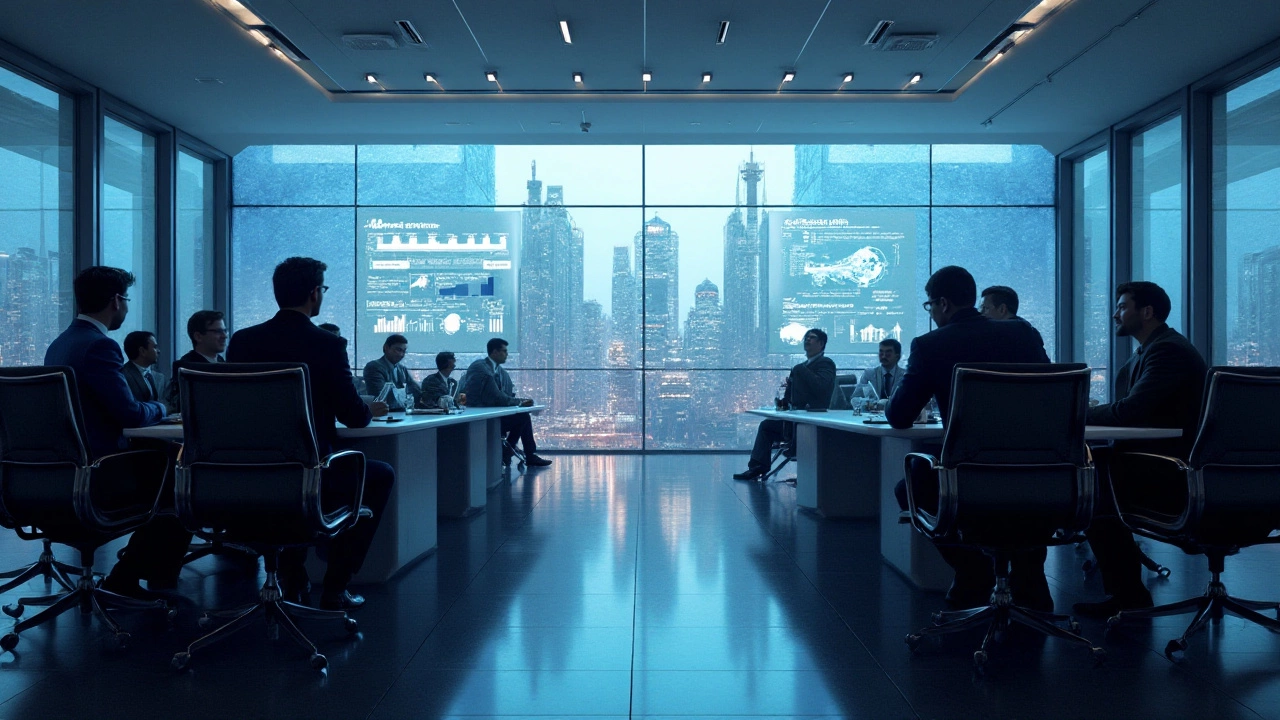
Future of Steel Manufacturing
As we gaze into the future of steel manufacturing, the road ahead is paved with innovation and sustainability. With global demands steadily increasing, the industry is adapting at an unprecedented pace, driven by technological advancements and a growing emphasis on environmental stewardship. According to the World Steel Association, the industry's carbon footprint must reduce by 50% by 2050 to align with climate goals. This challenge pushes manufacturers to explore alternative production methods, such as hydrogen-based steelmaking and carbon capture and storage (CCS) technologies, which promise significant reductions in greenhouse gas emissions.
The shift towards digitalization marks another significant leap. Industry 4.0, a term that denotes the next phase of industrialization, introduces smart factories that leverage the Internet of Things (IoT), artificial intelligence (AI), and data analytics. These technologies offer predictive maintenance, real-time monitoring, and enhanced productivity, reshaping traditional production lines into highly efficient, interconnected systems. Companies investing in these technologies report not only greater efficiency but also considerable cost savings.
Material innovation is crucial in this era of change. Researchers are continuously developing new steel alloys that combine lightweight properties with exceptional strength, making them ideal for automotive and aerospace applications. The push for electric vehicles (EVs) has further accelerated this trend, as automakers demand materials that improve vehicle safety while enhancing energy efficiency. A cutting-edge example is the development of graphene-infused steel, touted for its incredible strength and conductivity, potentially revolutionizing numerous industrial applications.
Adapting to Global Challenges
The future of steel production is not without its challenges. Global supply chain disruptions, fluctuating raw material prices, and geopolitical tensions add layers of complexity that manufacturers must navigate. Flexibility and resilience become paramount as companies strive to mitigate risks and ensure the uninterrupted flow of resources. The adoption of circular economy principles, which aim to minimize waste and maximize resource efficiency, emerges as a strategic approach. Through recycling and reusing steel, the industry can reduce dependency on virgin raw materials and reinforce its sustainability commitment.
"The future of the steel industry lies in its ability to innovate and adapt to changing global demands while meeting its environmental commitments," stated Dr. Nicole Dunker, a leading expert in industrial sustainability at the International Energy Institute.
Collaborations between governments, academic institutions, and industry leaders pave the way for breakthroughs that will shape the steel landscape. Initiatives like the Clean Energy Ministerial's Industrial Deep Decarbonization Initiative (IDDI) foster an environment where knowledge exchange and joint ventures become instrumental in overcoming the industry's most pressing challenges. As the steel landscape evolves, staying ahead of the curve requires embracing change and viewing challenges as opportunities.