The world of plastic manufacturing is as vast as it is intricate, dominated by several powerhouse companies that have become household names through their innovations and wide-reaching products. These companies produce materials that touch every aspect of our daily lives, from packaging and automotive parts to healthcare supplies and electronics.
Understanding who these industry leaders are can offer insights into global economic flows and technological advancements. It's a sector constantly evolving, especially as environmental considerations rise to the forefront of global discussion. In this exploration, we delve into the largest plastic manufacturers, their market strategies, and how they balance efficiency with sustainability.
- Leading Companies Overview
- Market Influence and Strategies
- Innovations and Technologies
- Environmental Challenges and Sustainability
- Future Trends and Predictions
Leading Companies Overview
In the ever-expanding realm of plastic manufacturing, a few giants hold sway, steering the industry through innovations and strategic maneuvers. Among them, BASF SE, the German conglomerate, stands out not just for its scale of operations but for its commitment to developing advanced plastic solutions. Established in 1865, BASF has evolved into a leader, impacting various sectors from automotive to electronics. Their focus on sustainability is noteworthy, with numerous initiatives aimed at reducing carbon footprints in plastic production. This broad reach positions them not only as a key industrial player but also as a force pushing for environmental responsibility.
Joining BASF at the top is Dow, another behemoth in the chemical and plastics market. Headquartered in the United States, Dow leverages extensive research facilities to maintain its edge. Through constant innovation, they enhance product durability and efficiency, ensuring that their plastic products meet evolving consumer demands. Their collaborations with technology firms and investment in recycling technologies set them apart, demonstrating a commitment to a circular economy. "Our aim is to achieve 100% recyclable materials in all new product lines by 2035," a Dow spokesperson stated at a recent industry summit. Such clear goals underscore their forward-thinking approach and influence over global markets.
Adding to the list is LyondellBasell Industries, renowned for its diverse plastic resins offering. This Netherlands-based company has carved a niche by blending high performance with sustainability, a crucial component for modern demands. They operate some of the largest polymers production plants worldwide, enabling access to a myriad of applications. Their strategy of expanding into emerging markets and continual investment in eco-friendly technologies showcases their ambition. Interestingly, LyondellBasell has also instituted a program aiming at curtailing plastic waste, reflecting industry trends towards environmental consciousness.
Another significant player is Reliance Industries, representing the burgeoning industrial capabilities of India. Reliance has marked its presence globally by amplifying production capacities and focusing on diverse product offerings. Their sheer scale and distribution networks facilitate an extensive reach, driving growth not just in domestic territories but also internationally. The company's efforts towards integrating renewable energy into their manufacturing processes are testament to their versatile strategy.
In an industry where change is constant, these companies exemplify adaptability and foresight. The leaders are not only defined by current success metrics but also by their ability to forecast market changes and gear up for future challenges. From sustainability programs and technological advancements to global partnerships, these manufacturers are paving the way with resilient business models. As plastic remains integral to modern economies, understanding these companies offers a window into future industry developments and trends.
Market Influence and Strategies
The global plastic companies dominate the industry with their strategic maneuvers and market penetration techniques. These industry titans are instrumental in meeting the burgeoning demands for plastic, aligning their production strategies with emerging market trends. Their approach is often multifaceted, leveraging innovation, brand loyalty, and vast distribution networks. Many of these companies are headquartered in regions close to the raw materials, which cuts transportation costs and enhances supply chain efficacy.
One effective strategy employed by leading plastic manufacturers is the focus on specialized high-performance plastics, which have applications in aerospace, electronics, and healthcare. This specialization not only opens up high-profit margins but also ensures that these companies stay ahead in technology. By investing significantly in research and development, they continuously enhance their product offerings, making sure they are both durable and eco-friendly.
Another critical aspect of their strategy is adapting to regulatory standards. With governments worldwide imposing stricter regulations on plastics to curb pollution, these companies proactively alter production processes. This involves investing in technologies like biodegradable plastics and recycling methods, which can be observed in countries like Germany and Japan, where recycling rates are exceedingly high.
"Embracing sustainability doesn’t just stop at recycling. It’s ingrained in every product we design, every process we deploy," says a leading executive from BASF, a top player in the industry.
Market influence is also wielded through strategic mergers and acquisitions. By absorbing smaller competitors and niche players, larger companies consolidate market power and broaden their product portfolios. This tactic not only reduces competition but also provides technological and geographical advantages. For instance, when Dow merged with DuPont, it created a behemoth in the materials science industry, further solidifying its stance as a leader in plastic manufacturing.
Finally, these companies adeptly navigate economic fluctuations with agility. Their expansive global footprint allows them to shift production bases as needed, optimizing costs and meeting regional demands efficiently. This dynamic market presence ensures they remain resilient in volatile economic conditions, thus maintaining a stronghold in the international market.
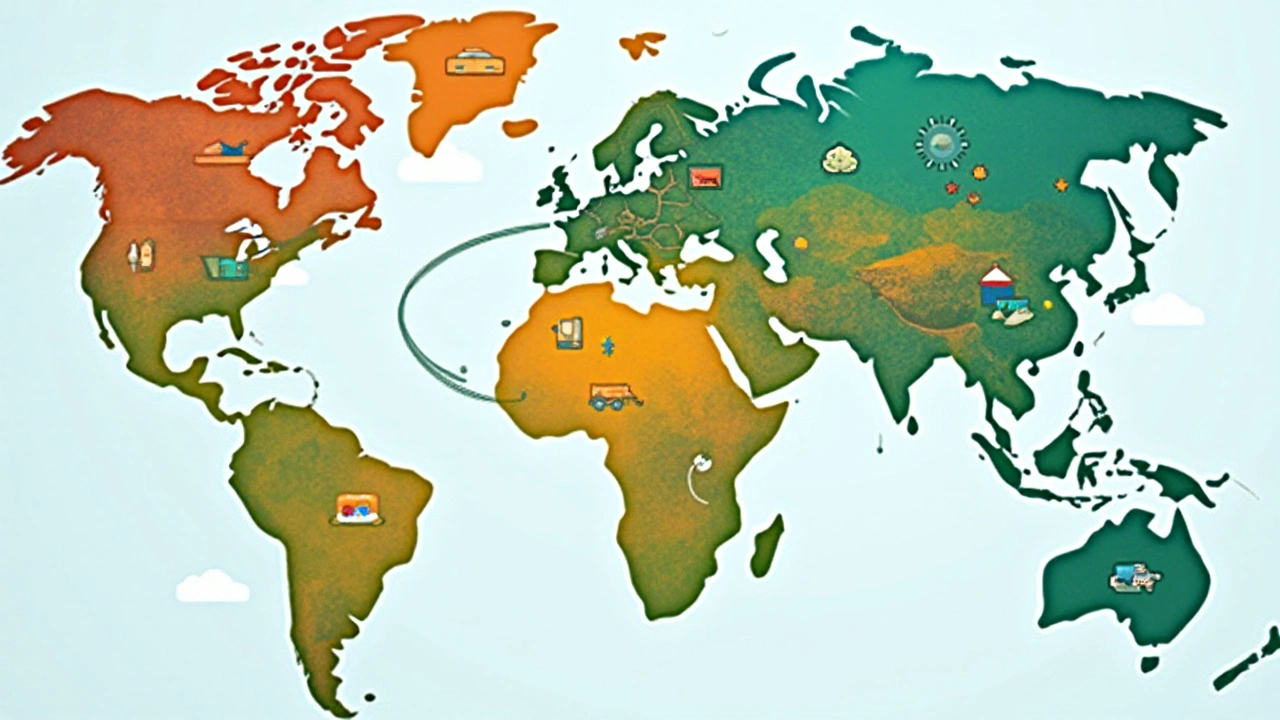
Innovations and Technologies
In the dynamic world of plastic manufacturing, innovation is both a driver of growth and a necessity for survival in an increasingly competitive market. Leading companies are not just responding to demand but shaping the future landscape of the industry through cutting-edge technologies. A remarkable advancement is the integration of biodegradable materials that promise to revolutionize sustainable packaging solutions. These innovations are transforming how we think about plastic, especially in reducing environmental impact. Bioplastics made from plant materials such as corn starch and sugarcane are gaining traction, leading to a new era where elasticity and strength do not compromise sustainability. Experts in the field predict that by 2030, bioplastics could make up a larger portion of the global plastics market, signaling a positive shift towards greener alternatives.
Digital transformation is another key area where companies are focusing their efforts. The rise of Industry 4.0 technologies, including the Internet of Things (IoT), artificial intelligence (AI), and big data analytics, has disrupted traditional manufacturing processes. These technologies enable real-time monitoring and predictive maintenance, which dramatically increase operational efficiency and reduce waste. This not only cuts costs but also enhances the quality of plastic products. Companies leveraging these technologies can provide better customization options for clients, effectively responding to the varied demands of different industries, from automotive to healthcare.
"Embracing digital transformation is no longer optional—it’s a necessity," says John Davidson, a prominent industry analyst.
3D printing stands at the forefront of technological advancements in plastic production. It offers unprecedented design flexibility, enabling rapid prototyping and the ability to produce complex structures that were once deemed impossible with traditional manufacturing. Innovators in this space are developing new printer filaments that drastically reduce production time and material waste, making it a cost-effective option for numerous applications. Additionally, collaboration within tech and material sectors has led to hybrid materials that combine the best qualities of traditional plastics with advanced composites. This innovation brings about stronger, lightweight materials ideal for aerospace and automotive industries. The potential for 3D printing to revolutionize custom parts production is vast and is only beginning to be tapped.
With all these advancements, it's crucial to acknowledge the continuous research and development (R&D) investments happening within the industry. Companies that commit significant resources to R&D often become pioneers of new plastic technologies. Collaborative efforts between academia and industry bring innovation from the lab to the market, addressing both current and future challenges. A strategic focus on advancing technologies not only secures a company's competitive advantage but also helps navigate regulatory challenges. These efforts are essential in creating solutions that align with global sustainability goals while catering to diverse market needs, ensuring a resilient future for the industry.
Environmental Challenges and Sustainability
The plastic manufacturing industry faces significant environmental challenges as it grapples with the residues of decades of production that have contributed to pollution and ecosystem disruptions. Plastics, while immensely versatile and durable, are not easily degradable, leading to long-term environmental burdens that companies today are working hard to mitigate. From oceans teeming with microplastics to landfills brimming with non-biodegradable waste, the industry is at a crossroads where innovation and sustainability must converge.
Many of the largest plastic manufacturers are investing heavily in research and development to create more sustainable products. This includes the development of biodegradable plastics and the implementation of circular economy principles. The circular economy concept—a response to the traditional linear economy of make, use, dispose—has gained traction among industry leaders looking to reduce waste. Companies are exploring methods to close the loop by integrating waste back into production processes as raw materials, thus curbing the environmental impact.
A key component of these efforts involves partnerships with governments and environmental organizations to craft regulations and initiatives that encourage reduced plastic usage and promote recycling. For instance, ExxonMobil, one of the top players in the field, has joined global alliances aiming to tackle plastic waste through cooperative strategies and commitments. Such initiatives reflect an industry-wide acknowledgment of the need for systemic change. Market demands also play a vital role as consumers increasingly prefer brands with sustainable practices.
"We've seen a greater consumer demand for more environmentally friendly solutions, and it's driving the market to innovate," said a spokesperson from the Plastics Industry Association.
Despite these advances, the transition to sustainable practices is hindered by significant hurdles. High costs related to new technologies and the sheer scale of shifting worldwide production systems can impede progress. The industry must also contend with varying regulations across different countries, which can complicate international compliance and innovation efforts. However, progress is being made with some companies introducing new products made entirely from recycled materials and aiming for net-zero emissions in their operations by the next decade.
The future of plastic manufacturing is heavily linked to sustainability, and as companies navigate these complex waters, the balance of ecological responsibility with economic feasibility remains delicate. Tracking these advancements and supporting transitions in practical ways—like opting for brands prioritizing sustainability—can contribute to broader environmental goals. It's a critical journey where every step counts, and each stakeholder from industry titans to end consumers plays a pivotal role.
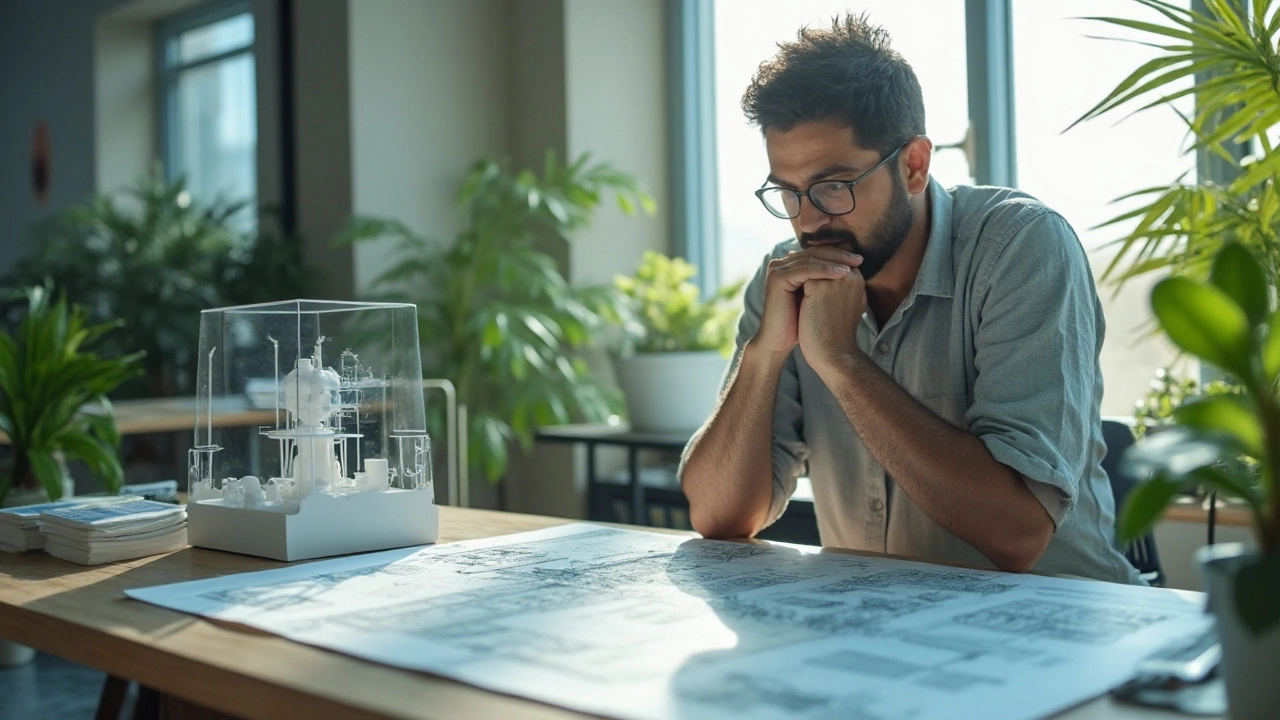
Future Trends and Predictions
The future of plastic manufacturers is undeniably intertwined with sustainability and technological innovation. As global concerns about plastic pollution amplify, the industry is undergoing significant transformations. Companies are pushing the boundaries of technology to develop bio-based plastics, which promise to reduce the dependency on fossil fuels and lessen environmental impact. These bioplastics, derived from renewable sources like corn starch or sugarcane, are making inroads into various sectors including packaging and consumer goods. This innovation is not just a trend but a necessity, as consumers become more environmentally conscious and demand eco-friendly alternatives.
One of the major predictions in the industry is the rise of circular economy practices. Global plastic companies are increasingly investing in methods that focus on recycling and upcycling. The idea is to create materials that not only sustain themselves through multiple life-cycles but also maintain quality and utility. This approach not only reduces waste but also mitigates the extraction demand for raw materials. A report by Plastics Europe suggests that even a 5% increase in recycling rates in the next decade could save industries billions annually, showing the financial viability as well as the environmental necessity.
"As we look towards a more sustainable future, the industry must reimagine its role in the global supply chain," says Sarah Jones, a leading environmental scientist. "Innovative solutions and aggressive adoption of circular economy principles will dictate the success of these companies in mitigating climate change impacts."
Digital transformation also plays a vital part in shaping future trends. Advanced technologies such as the Internet of Things (IoT) and Artificial Intelligence (AI) are being integrated into manufacturing processes. These technologies enhance process automation, increase precision, reduce waste, and ultimately, improve overall efficiency. This evolution helps companies stay competitive and responsive to the ever-growing market demands. With AI, predictive maintenance and quality checks become more efficient, reducing downtime and ensuring products meet stringent standards.
In the realm of packaging, the emergence of smart packaging solutions is expected to grow significantly. Smart packages, equipped with sensors and labels that can monitor the freshness of contents, provide real-time information about the condition of the product. Such innovations not only enhance consumer experience but also reduce wastage along supply chains, aligning perfectly with the sustainability goals of modern plastic manufacturers. A survey conducted by Grand View Research highlighted that the smart packaging market could grow at a Compound Annual Growth Rate (CAGR) of over 9% until 2030, reflecting substantial industry shifts.
As we move ahead, the challenge for industry leaders will be to balance these innovations with regulatory standards. Governments across the world are tightening regulations to curb pollution and encourage the use of sustainable materials. Companies that adapt proactively not only comply with these regulations but also gain market leadership by attracting environmentally conscious consumers. This adaptive approach ensures that these businesses remain in the vanguard, providing both eco-friendly and economically sound solutions for the global markets. Therefore, the future of plastic manufacturing is marked by strategic transformations aimed at sustainability and efficiency through state-of-the-art innovations.