If you ask most people what US city leads in steel, they'll probably blurt out "Pittsburgh." That made sense for a long time—steel plants blanketed western Pennsylvania, and names like Carnegie were everywhere. But right now, the old giants aren't running the show. The big action has shifted, and it's moved way beyond the smoky riverbanks of the old days.
Today, places like Gary, Indiana, are pumping out more steel than anywhere else. Drive around Northwest Indiana and you'll spot towers, smokestacks, and a skyline that's built on steel. US Steel’s Gary Works? That's the biggest steel mill in North America by tonnage. Add Cleveland-Cliffs facilities and Nucor’s high-tech plants down South, and you’ve got a hot competition for the top spot.
Steel is heavy, expensive to move, and needs lots of power to produce. That’s why steel cities pop up near ore, water, railroads, and cheap electricity. When you put those pieces together, it’s not always the cities you expect that come out ahead these days. Which city really dominates? Depends how you look at the numbers—and what you're counting. It's a way different landscape than it was even ten years ago.
- The Classic Steel Titans: Past and Present
- Meet the New Heavyweights: Emerging Steel Cities
- Why Location Matters: Secrets Behind Steel City Success
- Cutting-Edge Plants Changing the Game
- What It Means for Jobs, Prices, and the Future
The Classic Steel Titans: Past and Present
If you rewind to the early 1900s, steel production in the US was pretty much defined by a few powerhouse cities. Pittsburgh stood out. This city was pumping out half the nation’s steel at one point. The rivers made it easy to haul ore in, steel out, and no other US city even came close for decades. Carnegie Steel, which later became U.S. Steel, set up shop here and basically made Pittsburgh famous around the globe for steel.
But it wasn’t just Pittsburgh. Bethlehem, Pennsylvania, and Youngstown, Ohio, played huge roles too. Bethlehem Steel built everything from the Golden Gate Bridge to major warships in World War II. Back in the 1950s, Youngstown had more steel mills than grocery stores—it was that central to American industry.
Fast forward to today and the picture has changed. Those smokestacks and blast furnaces? Many are silent or gone. By the 1980s, foreign competition and new production tech cut deep into these cities’ steel business. Pittsburgh shifted toward healthcare and tech, Youngstown faced factory shutdowns, and Bethlehem’s steel mills closed after almost 140 years.
- Pittsburgh: Used to produce 60% of all US steel in its golden years
- Bethlehem: Home to the nation’s second-largest steel producer through most of the 1900s
- Youngstown: Known for having a large cluster of integrated steel mills
While these cities lost some of their swagger in steel manufacturing, their old mills and worker communities are a big reason why the US still plays a major global role. The legacy of these classic cities can be seen in today’s industry, but the actual center has moved—big time.
City | Peak Steel Production (million tons/year) | Current Key Industry |
---|---|---|
Pittsburgh | Over 30 | Healthcare, Tech |
Bethlehem | 10 | Tourism, Light Industry |
Youngstown | 6 | Distribution, Additive Manufacturing |
Meet the New Heavyweights: Emerging Steel Cities
The steel production map in the US is getting a big update. While folks still picture Pittsburgh steel, the action is hotter in places like Indiana, Alabama, and even Arkansas. Let’s take a look at who’s punching above their weight now.
Gary, Indiana, still leads the pack. US Steel’s Gary Works puts out more raw steel than any facility in America. It’s built right by Lake Michigan, so the plant can ship in iron ore cheaply by boat. Plus, workers and robust rail lines feed directly into Chicago’s huge manufacturing market.
Another name that keeps coming up? Mobile, Alabama. Steel giant AM/NS Calvert runs one of the world's most advanced steel finishing plants there. Since 2014, they’ve been making high-end flat-rolled steel that goes into things like cars and appliances. Why Alabama? Cheap natural gas and speedy shipping via the Gulf.
Now, check out Arkansas. The town of Osceola, not exactly a big headline name, is quickly turning heads. Nucor and Big River Steel—now owned by US Steel—both set up shop here, churning out high-grade steel using electric arc furnaces. These are less polluting and gobble up scrap metal for recycling. In 2023 alone, Osceola’s mills produced over 6 million tons of steel.
Here’s how a few emerging steel manufacturing plants stack up:
City | Main Plant(s) | Annual Output (Million Tons, 2023) |
---|---|---|
Gary, IN | US Steel Gary Works | 7.5 |
Osceola, AR | Nucor, Big River Steel | 6.1 |
Calvert, AL | AM/NS Calvert | 5.3 |
Cleveland, Ohio and Youngstown, Ohio still make a ton of steel too, mostly via Cleveland-Cliffs. But when you talk “emerging cities,” it’s those newer Southern and Midwest spots getting major upgrades and investments.
Why are they rising? For one, states like Arkansas and Alabama offer tax breaks, cheap land, and a workforce that’s eager for steady factory jobs. Plus, energy is less expensive, and ports like Mobile can ship steel out fast. So, the next time someone thinks about US steel, they shouldn’t just look east—they should check the map and watch places like Gary, Calvert, and Osceola eat up more of the action.
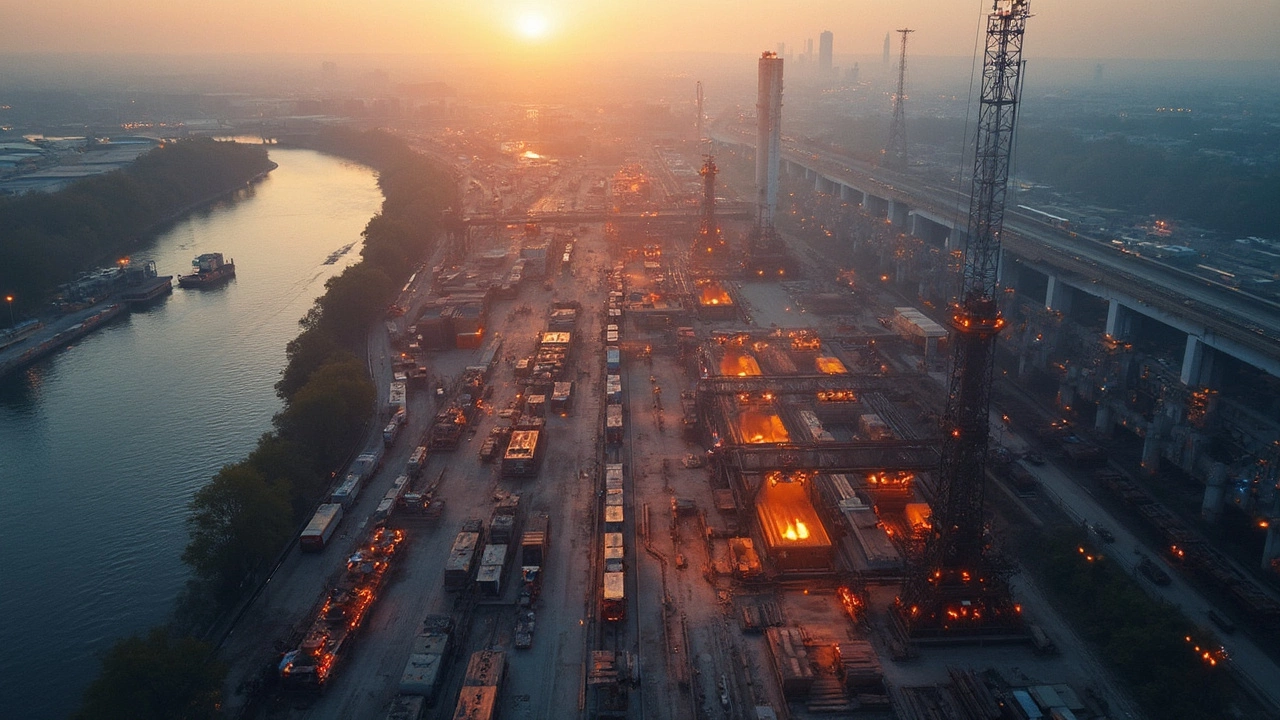
Why Location Matters: Secrets Behind Steel City Success
Ever wonder why some cities just click for steel production and others don’t? There’s a perfect mix: raw materials, strong transport links, and cheap power all need to be close. No steel mill wants to waste money hauling iron ore or coal across three states. So the best cities end up where everything lines up for fast, cost-effective work.
Take Gary, Indiana. It’s right on Lake Michigan, so it gets easy shipping by water. Plus, it’s at a crossroads of major rail lines and highways. That means steel plants here keep raw materials flowing in and finished steel shipping out, 24/7. Plants in this area can connect quickly to automakers in Detroit or construction projects in Chicago. That local edge can drop transport costs by up to 20% compared to inland spots.
If you check out the Southeast, places like Birmingham, Alabama, built their legacy on natural deposits of iron ore and coal right in their backyard. Now, cities like Memphis and Decatur attract new steel manufacturing plants for another reason—cheap electricity from regional utilities and fast logistics thanks to inland ports on the Mississippi River. Nucor, one of the biggest US steel companies, picked these places for their scrap metal supply and low energy costs.
- Raw materials: Proximity to iron ore, coal, or scrap metal cuts costs.
- Transport: Cities near railroad, river, or highway hubs move steel out faster.
- Energy: Reliable, cheap power means lower bills for intense melting and forging.
- Customers: Being close to carmakers, construction, and appliance factories keeps demand high and delivery times low.
Check the powerhouse cities in steel these days, and you’ll notice they don’t just have one of these advantages—they usually have three or four.
City | Main Advantage | Major Facilities |
---|---|---|
Gary, IN | Lake access, close to Midwest factories | US Steel Gary Works |
Cleveland, OH | Great Lakes port, big labor pool | Cleveland-Cliffs |
Decatur, AL | Cheap power, near scrap sources | Nucor Steel Decatur |
Memphis, TN | River access, logistic hub | Nucor Memphis |
The truth is, the steel industry always follows the path of least resistance. If a city checks the right boxes, it's almost guaranteed to draw in new or expanded steel mills. And if those advantages fade—plants pack up and move where the action is hotter.
Cutting-Edge Plants Changing the Game
If you haven’t checked out a modern steel manufacturing plant lately, you might be surprised. Forget the old images of endless smoke and clanging machines—new factories look more like tech labs. Places like the Nucor plant in Brandenburg, Kentucky or Cleveland-Cliffs' Direct Reduction Plant in Toledo aren’t just big, they're smart. They use computers, robots, and even AI to crank out stronger steel with less waste and way lower emissions.
Some plants run electric arc furnaces, which are cleaner and more flexible than the blast furnaces of the past. More than 70% of US steel is now made using recycled scrap instead of raw iron ore, mostly thanks to these new electric setups. This isn’t just good for the planet—it’s also cheaper and faster.
- Nucor (Brandenburg, KY): This place specializes in heavy steel plates used for wind towers, bridges, and military armor. It opened in late 2023 and can produce up to 1.2 million tons each year.
- Cleveland-Cliffs (Toledo, OH): Their direct reduction plant is the first of its scale in the US, and it feeds cleaner iron into their steel mills. It's a key part of the company's aim to cut carbon emissions.
- US Steel (Osceola, AR): Their Big River Steel facility is called a "mini mill" but makes millions of tons a year using state-of-the-art recycling technology.
Check out these numbers from 2024—they show how the new-style steel production plants stack up:
Plant Name | Location | Type | Annual Output (tons) |
---|---|---|---|
Nucor Brandenburg | Kentucky | Electric Arc Furnace | 1,200,000 |
Cleveland-Cliffs DRI | Ohio | Direct Reduction | 1,900,000 |
Big River Steel (US Steel) | Arkansas | Recycling Mill | 3,300,000 |
Bottom line—these new plants don’t just make more steel, they do it faster and with a lot less pollution. Anyone interested in modern steel production should keep an eye on these spots. If you’re thinking careers, investing, or even tech partnerships, these cities are where the action is now.
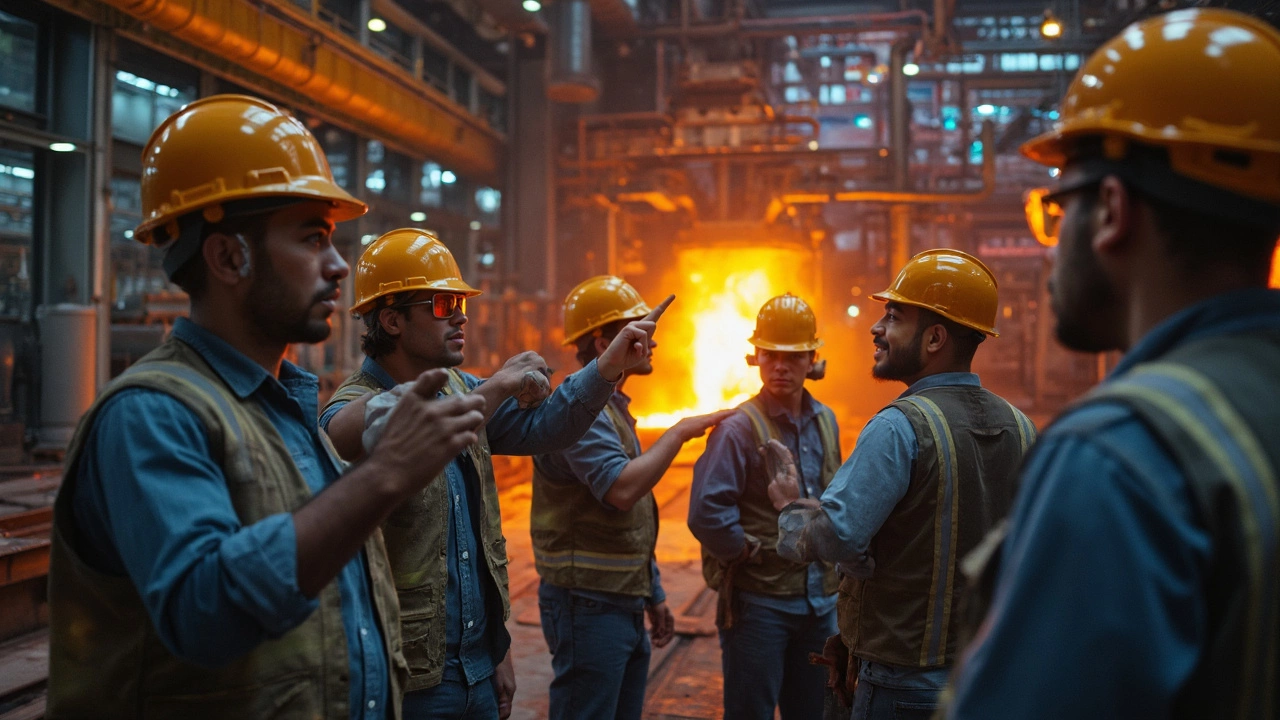
What It Means for Jobs, Prices, and the Future
When you’re talking about steel production in the US, it’s really a story about jobs first. Places like Gary, Indiana, and nearby towns have entire communities built around these steel manufacturing plants. US Steel’s Gary Works alone has employed thousands for over a century—at its peak, over 30,000 workers, and even today, it's a major employer in the region. Mill jobs pay more than many other hourly gigs, often with solid benefits, which means these plants anchor local economies.
But there have been big changes. Most newer plants use fewer people, thanks to tech upgrades and automation. Someone running a control room today might do the work of what used to be ten people on the floor. Here’s a look at the shift in numbers at some major mills:
Location | Year | Number of Workers | Annual Output (Million Tons) |
---|---|---|---|
Gary Works (Indiana) | 1990 | 13,000 | 6.5 |
Gary Works (Indiana) | 2023 | 4,700 | 7.5 |
Nucor (Arkansas) | 2000 | 2,000 | 2.1 |
Nucor (Arkansas) | 2023 | 1,200 | 3.3 |
If you’ve got a family depending on those jobs, the future looks different. Plants are hiring—but for folks with technical skills, not just anyone off the street. Welding, robotics, and data science are skills that mean job security in today’s US steel world.
What about prices? Here’s the deal: Local steel mills mean cheaper steel for American manufacturers since there’s less shipping and fewer tariffs. That doesn’t always mean cheap prices at the hardware store, but it does help steady the market a bit. Global events, like wars or trade fights with China, can still send steel prices soaring in a flash.
Looking forward, cities winning at steel aren’t just manufacturing old-school beams. They’re putting out specialty, high-strength stuff for electric cars, wind turbines, and modern infrastructure. If you’re tracking where the next steel boom will hit, follow the companies pushing out these higher-value products.
Tips if you want to work in or around steel manufacturing plants:
- Get technical training, especially with robotics or materials science.
- Stay up to date. Plants are modernizing, and old skills aren’t always enough.
- Some plants run 24/7 shifts—be ready for night and weekend hours.
- Many facilities partner with local trade schools; check out those programs for quick entry.
For cities, more steel work means better infrastructure spending, higher tax revenues, and more small business growth. But it also means grappling with automation and making sure the next generation is ready for jobs that look nothing like their parents’ old mill work.