Manufacturing is the backbone of modern industry, providing essential goods and services to meet the needs of societies worldwide. As we step into 2025, the landscape of manufacturing is as dynamic as ever, shaped by relentless innovations and economic shifts. To truly grasp this vital sector's present and future, we must understand the two leading forms: discrete and process manufacturing.
Each type offers something unique, from the way they are implemented to their specific applications and benefits. While discrete manufacturing deals with production of distinct items, like automobiles and electronics, process manufacturing involves creating goods that are blended or processed, such as in the chemical or food industry. This difference not only affects the production methods but also how businesses interact with governmental support and schemes tailored to boost manufacturing growth.
- Introduction to Manufacturing Types
- Discrete Manufacturing Explained
- Process Manufacturing Fundamentals
- Government Schemes Supporting Manufacturing
- Future Trends in Manufacturing
Introduction to Manufacturing Types
The world of manufacturing is as expansive as it is integral to our everyday lives, channeling raw materials into the products that fuel our modern existence. When we delve into this domain, we encounter the primary classifications of manufacturing types. These types dictate not only the procedures undertaken on the factory floor but also influence the broader industrial strategies that businesses adopt. As we explore these classifications, it's imperative to understand how they develop uniquely tailored production methods that allow for specialization and efficiency.
Manufacturing, in its essence, is the transformation of raw materials into finished goods, but the methods by which these transformations occur can vary significantly. Two distinct systems dominate the field: discrete manufacturing and process manufacturing. Discrete manufacturing is characterized by the assembly of individual parts and pieces to form a complete product, often seen in sectors producing automobiles, electronics, and appliances. This manufacturing type thrives on a framework allowing for the customization and adjustment of individual units, leading to unique end products that often can be disassembled or modified after production.
Conversely, process manufacturing operates on a different wavelength. It is ingrained in industries where products are formulated or synthesized through chemical or physical transformations. Think pharmaceuticals, food, and beverages – once a product is produced, it cannot be broken down into its original components. This type of manufacturing often involves complex formulations, where the properties of the raw materials are fundamentally altered to achieve the desired outcome. The transition from raw to final product is seamless, which requires a tightly controlled and consistent production environment to ensure quality.
In an insightful analysis, industry expert John Anderson noted,
"The evolution of manufacturing processes reflects not only technological advancement but a nuanced understanding of market needs, pushing companies to finely tune their operations across distinct manufacturing paradigms."His observation underscores the importance of adapting manufacturing strategies to fit the broader goals of efficiency and innovation.
It is also crucial to recognize that these manufacturing types are not just operational definitions but deeply embedded within the economic and policy frameworks governing industrial activity. Government schemes, designed to bolster the industry, often focus on these classifications to dispel specific support mechanisms. Such initiatives not only enhance productivity but also ensure these industries can evolve with technological advances. By tailoring government backing to specific manufacturing types, the potential for industry growth and sustainability is maximized.
Discrete Manufacturing Explained
At its core, discrete manufacturing is all about the creation of individual, distinct items. Think about the car you drive, the furniture in your living room, or the smartphone in your pocket—each of these is a product of discrete manufacturing. This type of manufacturing relies heavily on assembly lines, where components are often put together piece by piece to form a final product. It's akin to putting together a complex jigsaw puzzle, where each part must fit perfectly to ensure the whole is functional and meets predefined quality standards.
One of the most significant characteristics of discrete manufacturing is its reliance on a Bill of Materials (BOM). This detailed list outlines every component and part required during the manufacturing process, from nuts and bolts to the smallest microchip in a piece of technology. Each item on the BOM is produced or sourced with precision, ensuring that all parts are ready and available as the product moves along the assembly line. It's not uncommon for discrete manufacturing facilities to produce a wide range of products, often necessitating flexible processes and adaptable machinery that can switch from producing one product to another with ease.
"Effective discrete manufacturing pivots around the meticulous orchestration of assembly and the seamless integration of various components into a cohesive whole," says Chris Anderson, an industry expert and author on manufacturing systems. "Without a robust system in place, even slight deviations can lead to significant inefficiencies and product defects."
Advancements in technology, such as robotics and automation, have propelled discrete manufacturing forward. Automation tools are now indispensable, not only in assembling components but also in ensuring flawless quality control and efficient logistical operations. This high level of automation reduces human error and speeds up production processes immensely, a crucial factor given the demand for high-quality, mass-produced goods in today's market.
Specific industries that thrive on discrete manufacturing processes include automotive, aerospace, electronics, and consumer goods sectors. Each of these sectors demands an astute understanding of intricate designs, materials, and engineering excellence. Automobiles, for instance, require an understanding of various materials like metals and plastics, precise engineering for engines, and the integration of advanced technologies for modern vehicles. This complexity is mirrored in the aerospace industry, which requires stringent compliance with safety regulations and exceptional performance standards.
Another key aspect of discrete manufacturing is customization. The modern market is heavily driven by consumer demand for personalized products. This trend has pushed manufacturers to adopt lean manufacturing techniques, focused on reducing waste and enhancing the ability to produce bespoke items without sacrificing efficiency or quality. The agile approach to production processes means manufacturers can swiftly adapt to changing consumer trends and continue to ensure that each product is exactly what the customer desires.
Discrete manufacturing plays a critical role in the context of government schemes dedicated to boosting industrial growth. These schemes often provide incentives for technological enhancements, workforce training, and research in manufacturing technologies. For businesses, this means a plethora of opportunities to innovate, invest in state-of-the-art machinery, and build a more skilled workforce ready to tackle future challenges in the manufacturing sector.
A 2023 report highlighted that companies leveraging discrete manufacturing techniques were found to have a competitive edge, with increased production rates of up to 20% compared to traditional methods. Embracing innovation in discrete manufacturing not only ensures product quality and variety but also positions companies strategically for sustained economic success and alignment with national industrial policies.
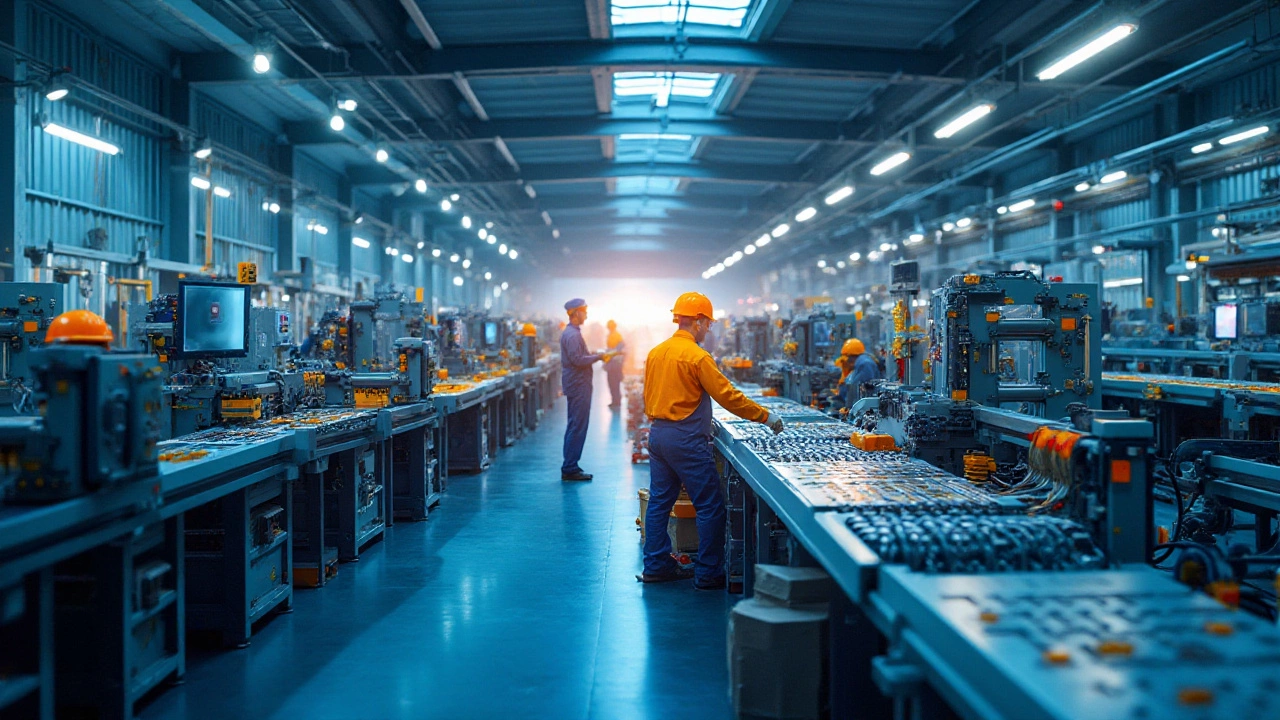
Process Manufacturing Fundamentals
Process manufacturing is a fascinating sector of industry that revolves around the transformation of raw materials into finished goods through a series of chemical, physical, or mechanical means. Unlike discrete manufacturing, where the focus is on assembling distinct entities, process manufacturing results in products that are indistinguishable in their final form. Common sectors that utilize this approach include pharmaceuticals, food and beverages, oil and gas, chemicals, and many others. In these industries, the final product emerges from the continuous or batch production processes, leading to a consistent and uniform output.
One of the defining features of process manufacturing is its reliance on formulas or recipes, rather than bill of materials (BOM). For instance, in the creation of a beverage, the production line follows a recipe that dictates the precise mix of ingredients. This approach ensures every batch of soda, juice, or fermented drink tastes the same, regardless of when or where it’s produced. The significance of a standardized recipe cannot be overstated, as it guarantees not only quality but also regulatory compliance, especially when dealing with consumables and pharmaceuticals, where safety is paramount.
The role of technology in enhancing process manufacturing cannot be overlooked. With the advent of Industry 4.0, these production lines have transformed dramatically. Automation, IoT (Internet of Things), and AI (Artificial Intelligence) have revolutionized traditional methods by increasing efficiency and reducing waste. Machines now communicate with each other throughout the manufacturing plant, predicting maintenance needs and minimizing downtime. For example, embedded sensors within the equipment monitor the viscosity and temperature of liquids continuously, ensuring that every bottle of syrup is identical in flavor and consistency.
Process manufacturing also poses unique challenges, particularly in waste management and sustainability. The objective is to optimize resource usage and minimize by-products or emissions that might harm the environment. Companies have increasingly adopted sustainable practices, using renewable energy sources and recycling processes to mitigate their environmental footprint. This aligns with numerous government schemes promoting greener methods across manufacturing sectors. As William J. Baumol once said,
"Innovation in manufacturing represents a key path to recovering environmental sustainability."This wisdom resonates loudly today, as companies aim to address ecological concerns through innovative solutions.
An intriguing aspect is the economics of scale often associated with process manufacturing. Large-scale operations tend to produce more cost-efficient products due to the streamlined nature of bulk manufacturing — an economic advantage that smaller operations find hard to match. However, this scale requires robust infrastructure and often significant initial investment, laying a high entry barrier. To offset these costs, many governments offer subsidies or tax incentives, acknowledging the essential role of process manufacturing in industrial sectors and the economy.
For a clearer understanding, consider the longstanding wine industry as an emblematic case of process manufacturing. Here, the fermentation process dictates the texture, taste, and quality of the wine. Each step is critical, from grape selection to maturation, controlled carefully by a blend of traditional knowledge and modern science. This ensures the industry can meet a global demand that spans regional and cultural boundaries, with the added benefit of modern sustainability practices. Hampering this process with unnecessary interruptions can spell disaster for consistency and quality, illustrating just how meticulous process manufacturing truly is.
Government Schemes Supporting Manufacturing
In recent years, global economic landscapes have shifted dramatically, making government support crucial for sustaining and advancing the manufacturing sector. For countries to remain competitive on a global scale, government initiatives are not just beneficial but necessary. These schemes often focus on enhancing productivity, fostering innovation, and ensuring the sustainable growth of this vital industry. Governments worldwide recognize the importance of manufacturing to job creation and economic stability and have crafted policies reflecting these priorities. Manufacturers today can benefit from a tapestry of programs including tax incentives, grants, and infrastructural development designed to invigorate both discrete and process manufacturing sectors.
One prominent example is the development of the Manufacturing USA network in the United States. This initiative connects industry participants with federal agencies and research institutions, aiming to secure America’s future in global manufacturing. According to a report by the NAM, "Such collaborations have led to increased productivity by 20% in engaged enterprises." Across the Atlantic, the European Union has established significant funding channels under its Horizon Europe program, funneling billions into sustainable and innovative manufacturing practices. Asian economies are not left out, as seen in China’s Made in China 2025 plan which aims to revolutionize its manufacturing with an emphasis on integrated technologies and reduced environmental impact.
These schemes typically involve substantial financial resources aimed at facilitating research and development in cutting-edge manufacturing technologies. The focus often extends to enhancing digital manufacturing capabilities, thereby optimizing production flow. In addition, schemes target skill development, ensuring the workforce is aptly prepared to operate complex machinery and advanced manufacturing systems. Training programs, often subsidized or supplemented by government funds, play a significant role in this aspect.
Moreover, smaller manufacturing businesses are not sidelined in these initiatives. Specific schemes are crafted to support Small and Medium Enterprises (SMEs), recognizing their crucial role in economic diversification and job creation. As a part of these initiatives, governments may offer low-interest loans or grants specifically allocated for upgrading SME production facilities. There’s also a concerted effort to develop 'Manufacturing Clusters', which are geographic concentrations of interconnected businesses and institutions. These clusters receive infrastructural support that enhances collaboration, innovation, and efficiency within the manufacturing industry.
Another innovative approach seen globally is the establishment of 'Green Manufacturing Schemes', which prioritize sustainability alongside industrial growth. These initiatives promote a shift towards environmentally friendly materials and processes, supporting companies in reducing their carbon footprint and encouraging recycling and responsible waste management. Collaborating with educational institutions to drive research in sustainable manufacturing is a key feature of such schemes, with some governments offering prizes and awards for notable achievements in this domain.
It is evident that the success of these government schemes lies in their ability to adapt to changing industrial needs, ensuring they remain aligned with technological advancements and global economic shifts. The future of manufacturing will likely continue to be heavily influenced by such initiatives, as both discrete and process manufacturing industries strive to not only meet but anticipate market demands in a rapidly evolving world.
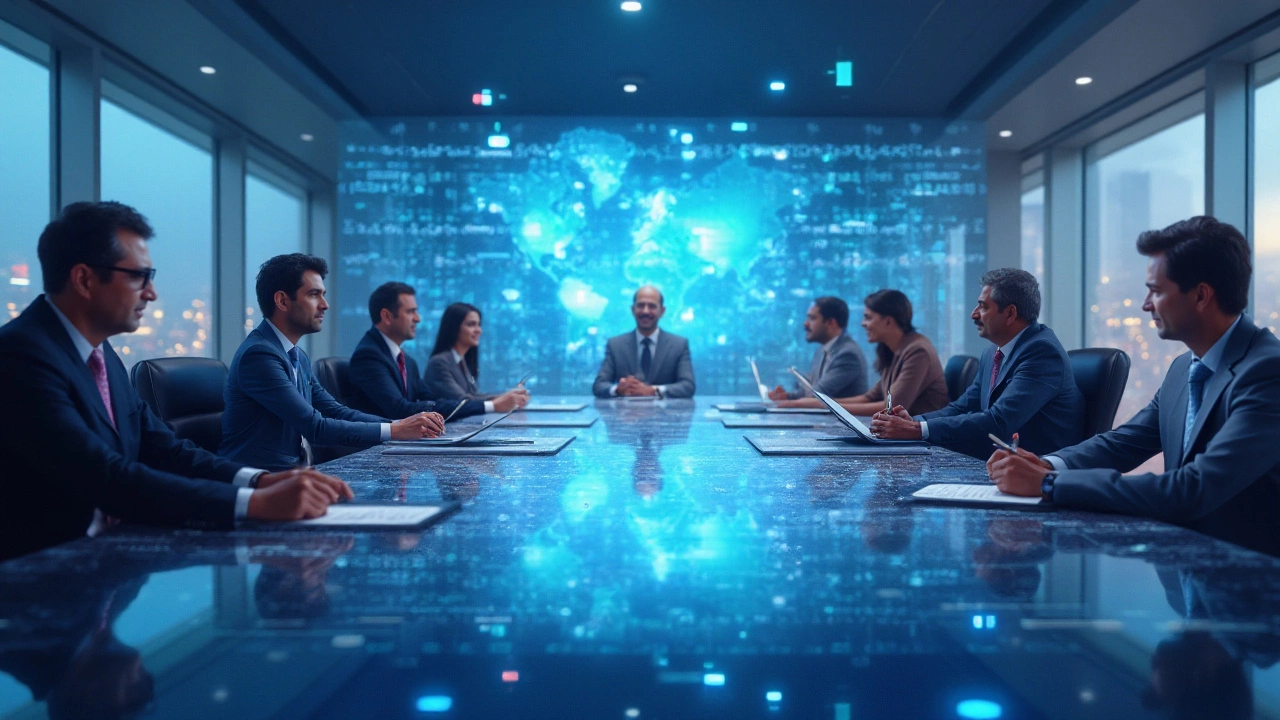
Future Trends in Manufacturing
The manufacturing industry stands at the brink of transformation as we head deeper into 2025. A surge in technological advancements is setting the stage for sweeping changes, promising to redefine how we perceive and conduct manufacturing operations. One notable trend is the rise of smart factories. Integrating technologies like the Internet of Things (IoT) and artificial intelligence (AI), these factories aim to improve efficiency and reduce waste. This transition to digital-first operations will likely decrease human error, streamline processes, and enhance production quality. These developments are reshaping the landscape, encouraging more industries to embrace a data-driven approach to manufacturing.
Decentralized manufacturing is also gaining traction. With a shift towards local production hubs, businesses are working to meet consumer demands more swiftly while cutting down on transportation costs and emissions. This movement aligns with growing environmental concerns and sustainability goals, pushing manufacturers to adopt greener practices. As environmental regulations become stricter worldwide, this trend is expected to become more prominent, transforming traditional supply chain dynamics.
Another significant trend is the integration of additive manufacturing, more popularly known as 3D printing. This technology allows for more intricate designs, rapid prototyping, and customization at an unprecedented scale. In particular, industries such as aerospace, healthcare, and automotive are already leveraging these capabilities to innovate and outpace their competition. This shift not only paves the way for innovation but also enhances the ability to create locally sourced products, tailored to specific market needs, thus aligning seamlessly with global sustainability efforts.
Moreover, workforce changes are unavoidable as automation takes center stage. While some fear job losses, the evolving landscape promises to create new career opportunities. Workers will require new skill sets focused on managing and optimizing technology-driven processes. Investing in workforce training and development is likely to become a priority for companies striving to keep up with advancements.
The influence of emerging economies in manufacturing can also not be overlooked. As regions like Southeast Asia become increasingly pivotal in the global supply chain, businesses are looking to tap into these markets for their cost advantages and growing local markets. This shift might see a more balanced distribution of manufacturing prowess across the globe. It's noteworthy that according to a McKinsey report, "By 2025, global consumption in emerging markets will reach $30 trillion, a staggering figure that represents nearly half the global total."
The convergence of all these trends is poised to reshape manufacturing, promoting a dynamic and responsive model primed for the challenges and opportunities of the future. Companies must remain agile, ready to adapt and innovate as the industry moves toward an exciting era of transformation.